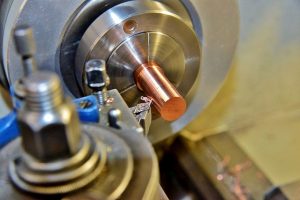
Manufacturing companies use a variety of machining processes to deform and shape metal workpieces, one of which is turning. Not to be confused with milling, turning is a machining process that involves the use of a stationary cutting tool to remove material from a rotating workpiece. As the cutting tool presses against the workpiece, it removes material, thereby changing the size and shape of the workpiece. Below are five fast facts about turning in the manufacturing industry.
#1) Performed Using One of the Oldest Machining Tools
Turning is performed using one of the world’s oldest machining tools, a lathe. A late is essentially a horizontal workbench that’s designed to hold, as well as rotate, a workpiece. There are different types of lathes, some of which use a different configuration of components. Regardless, they all hold and rotate a workpiece against a tool bit. Lathes are considered one of the world’s oldest machining tools, with origins dating back to 1300 B.C.
#2) Supports Diamond Cutting Tools
Some lathes support a diamond-tipped cutting tool. The term “diamond turning” refers to the use of a lathe with a diamond-tipped cutting tool. Diamonds, of course, are exceptionally strong. Therefore, they are able to cut through hard materials. Diamond turning is used to create lasers, telescopes and other optical products.
#3) Produces Swarf
Swarf is a byproduct that’s produced naturally during turning. Also known as chips, swarf consists of small pieces of metal. During turning, the lathe’s cutting tool will remove material from a workpiece. The workpiece will rotate against the cutting tool, which causes some of its material to be removed. This excess material is known as swarf or chips.
#4) Differs From Milling
Many people mistakenly assume that turning is the same milling. After all, both processes involve the use of a cutting tool to remove material from a workpiece. While similar, though, they aren’t the same. With turning, the cutting tool is stationary while the workpiece rotates. With milling, the cutting tool rotates while the workpiece is stationary. There are other nuances between these two machining processes, but that’s the primary way in which they differ.
#5) 3 Primary Turning Processes
All turning processes are defined by their use of a stationary cutting tool and a rotating workpiece. With that said, there are three primary types of turning process. This includes tapered turning, spherical turning and hard turning. Tapered turning is designed to create a cylindrical shape for the respective workpiece. Spherical turning, as you may have guessed, is designed to create a spherical shape for the respective workpiece. Hard turning, on the other hand, is used exclusively for workpieces made of exceptionally hard materials.