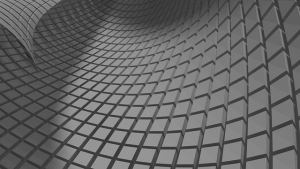
Have you heard of electron-beam melting (EBM). A form of additive manufacturing, it’s become an increasingly popular manufacturing process. Like other forms of additive manufacturing, it involves the use of a machine to build complex objects layer by layer. EBM, however, uses a unique approach that offers several noteworthy benefits. For a crash course on EBM and how it works, keep reading.
What Is EBM?
Also known as electron-beam additive manufacturing, EBM is an additive manufacturing process in which the raw material is fused using heat. It still follows the same basic approach as most other additive manufacturing process by depositing material onto layers. With that said, EBM exposes the raw material to heat from an electron beam, which causes it to fuse together.
While inside a vacuum chamber, the raw material is exposed to an electron beam. As the raw material melts, it fuses with the surrounding material that was previously deposited by the machine. EBM typically uses metal as the raw material. When exposed to the heat from an electron beam, the metal metals, at which point it fuses with the surrounding metal.
EBM vs Selective Laser Sintering: What’s the Difference?
Since they both involve heating the raw material, EBM is often confused with selective laser sintering. So, what’s the difference between these additive manufacturing processes? The main difference lies in the degree to which the raw material is melted. With EBM, the raw material is completely melted so that it fuses with the surrounding material. With laser sintering, the raw material is exposed to lesser heat so that it remains solid.
Advantages of EBM
EBM is a high-tech form of additive manufacturing that can quickly churn out new objects. According to Wikipedia, it can deposit up to 200 cubic inches of material per house. Of course, that’s significantly faster than the rate of deposition for other additive manufacturing processes.
In addition to being fast, EBM supports a wide variety of materials. Some of the most common materials used in this additive manufacturing process include stainless steel, high-carbon steel, cobalt, nickel, copper, titanium and various alloys. To say EBM is effective at fusing raw material would be an understatement. With its electron beam technology, it’s able to fuse even the toughest materials together. These are just a few advantages of EBM compared to other additive manufacturing processes.
Learn more about Monroe’s Additive Printing Service or get your parts printed now!
No tags for this post.