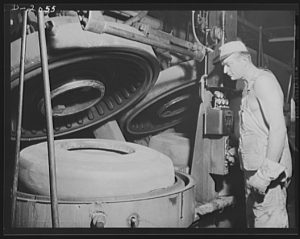
Vulcanization is a chemical treatment process that involves the application of chemicals — usually sulfur — to alter the physical properties of rubber. In its natural state, rubber has numerous attractive qualities, including rust, corrosion and mold resistance. But rubber is very soft and elastic, which can restrict its performance in certain applications. This has led some manufacturing companies to use vulcanized rubber to overcome this challenge.
History of Vulcanization
Vulcanization was invented by Charles Goodyear in 1839. In his patent, Goodyear described the process of using chemicals to change the physical properties of rubber. Goodyear also wrote about the use of additional chemicals to accelerate the vulcanization process at lower temperatures. Known as accelerators, these additional chemicals often include carbon or zinc.
Vulcanization Explained: What You Should Know
Vulcanization usually involves the application of sulfur. The 10th most abundant element in the universe, sulfur changes the physical properties of natural rubber as well as synthetic rubber. During a vulcanization process, rubber and sulfur, along with other chemicals, is heated to about 280 degrees to 350 degrees Fahrenheit in a pressurized mold. The combination of heat and chemicals forces the rubber to retract, and harden.
While sulfur is the most common curing medium used in vulcanization, other chemicals used in the process include:
- Peroxide
- Metal oxides
- Acetoxysilane
- Urethane
Countless rubber products and objects are vulcanized, some of which include O-rings, gaskets, seals and even tires.
The Impact of Vulcanization on Rubber
ScienceDirect explains that vulcanization changes the physical properties of rubber by forcing it to retract. Of course, there are mechanical methods that can force rubber to retract as well. The difference with vulcanization, however, is that it retains the original shape of the rubber. When vulcanization is performed on rubber, the rubber shrinks while retaining its original shape. Vulcanization essentially scales down rubber to a smaller size, all without deforming or altering its shape.
In addition to altering its size while retaining its shape, vulcanization also protects rubber from future deformation. As it’s shrunk, rubber hardens and becomes less vulnerable to deformation. It may still deform when exposed to enough stress, but vulcanized rubber won’t deform as easily as conventional, non-vulcanized rubber.
Rubber also becomes harder when vulcanized, which subsequently increases its tensile strength and reduces the risk of physical damage.
Unlike with thermoplastic chemical processes, the effects of vulcanization are permanent. After a rubber object or material has been vulcanized, it can’t be reversed.