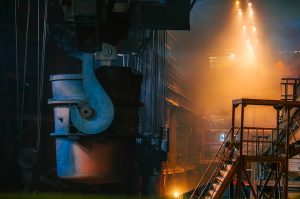
With origins dating back to around 3,200 B.C., casting is one of the oldest manufacturing processes that’s still used today. It’s used to create objects in a variety of shapes and sizes — and it supports the use of many different materials, including glass, plastics and metals. Continuous casting, however, is a unique form of casting that offers several key advantages over traditional casting processes.
What Is Continuous Casting?
Also known as strand casting, continuous casting is a multi-step casting process that involves the use of multiple rollers and molds to reshape and harden molten metal. Most casting processes are pretty basic, consisting of nothing more than pouring molten metal into a mold and allowing it to cool. Once cooled, the solidified metal is extracted from the mold. Continuous casting can also create three-dimensional objects out of molten metal, but it’s a more complex casting process that requires more work.
Continuous casting was invented during the mid-19th century. In 1857, English inventor Sir Henry Bessemer filed a patent for the world’s first casting process involving the use of multiple rollers.
Here are the basic steps of continuous casting:
- Metal is heated until it turns from a solid to a liquid, molten state.
- The molten metal is poured inside a tundish that routes it into the underlying mold.
- From there, the molten metal travels to a separate mold where it’s cooled to achieve a semi-solidified state.
- The shaped, semi-solidified metal is then routed to a strand guide with multiple rollers that stretches the metal.
- After being stretched, the metal is allowed to fully cool.
The Benefits of Continuous Casting
Statistics show that over hall of the world’s steel is produced using continuous casting. So, why do so many steelmakers prefer continuous casting over other casting processes? When used for producing metal ingots, including steel ingots, it’s able to eliminate problems caused by chemical variations. The molten metal is funneled through different molds and rollers to ensure an even and consistent chemical composition.
Continuous casting also ensures uniform production of metal objects. Whether a manufacturing company is producing 10 objects or 10,000 objects, they will all have the same size, shape and composition when this casting process is used. Since the molten metal remains semi-solid throughout much of the process, impurities are evenly distributed to prevent inconsistencies between the finished products.
Although it’s a more complex casting process, continuous casting is cost-effective for large-scale manufacturing applications. Using continuous casting, manufacturing companies can quickly produce large volumes of products in less time.