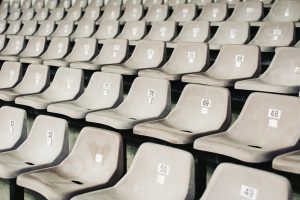
Dip molding is a process used to create a layer of plastic, usually polyvinyl chloride (PVC), over a metal object. Whether it’s steel, iron, copper, brass or aluminum, metal has different properties than plastic. Unlike plastic, for example, must metal corrodes when exposed to moisture. To protect against certain metal objects from corrosion — while also improving other characteristics of metal objects — manufacturers use dip molding.
Steps for Dip Molding
To dip mold an object, the mold is first heated and then submerged into the PVC material. Next, the mold is removed, drained and left to dry. Depending on the specific type of dip molding process used, the mold may then be cured. After the mold has finished drying and/or curing, the PVC shell be removed.
It’s important to note that dip molding often requires several cycles of submersion in the PCV material. If the PVC shell is too thin for the desired application, for example, the mold may be re-submerged into the PVC material. Each submersion adds a little more PVC material to the mold, making it thicker and thereby stronger and more durable.
Pros and Cons of Dip Molding
Dip molding has both advantages and disadvantages over other molding processes. It’s relatively inexpensive, for instance, allowing manufacturing companies to add a protective layer of plastic over their products or components without spending a fortune. The finished PVC shell is also easy to remove from the mold, as PVC material is naturally soft and somewhat elastic.
On the other hand, dip molding can be a time-consuming and tedious molding process. The PVC material must first be heated, and after dipping the mold into it, the mold be left to dry and/or cure. Furthermore, some manufacturing companies may have to submerge the mold into the liquid PVC several times to achieve the desired thickness.
Dip Molding vs Powder Coating
An alternative process used to create a plastic layer over metal objects is powder coating. While the results are similar, though, powder coating is a completely different process. With powder coating, a pressurized electrostatic spray gun is used to apply powder on an object. The electrostatically charged nature of the gun encourages the powder to bind to the object. After coating the surface in powder, the object is then moved to a kiln for curing. In comparison, dip molding is a simpler process that involves submerging a mold into heated, liquid PVC.