The Right Wheel For The Right Industry
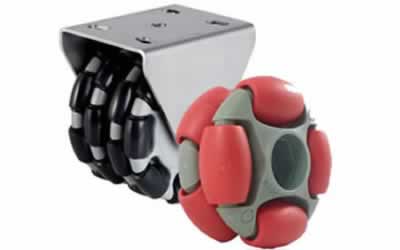
Hi-temperature RTH wheels are needed most in the food processing industry because these unique wheels and casters allow for Operating Temperature Ranges of -40°C (-104°F) to +260C (+500°F).
Traditional wheels do not work in hi-temp bakeries. Bakeries roll carts into ovens. Traditional hi-temp phenolic wheels survive about 350-400°F intermittent temperatures (thirty minutes in and thirty minutes cool-off). The traditional wheels are hard and noisy when rolling on the bakery floors. The wheels run directly on the caster axle without lubricant; they squeak when in higher temperatures.
An ergonomically friendly work environment requires noise reduction. RTH wheels are a special proprietary high temperature aerospace rubber compound that cushions the loaded racks from vibration, reduce floor noise, and can be equipped with special noise eliminating bearings. Jonathan Cuyler with Monroe said, “These hi-temp wheels are FDA/USDA approved for contact with food ingredients and are permanently lubricated with FDA approved, non-toxic lubricants.”
The RTH wheel has no odor when used in bakery hi-temp food processing applications; traditional cushion tread wheels usually emit a plastic or rubber foul smell when heated.
Frozen foods manufacturers find benefits from the hi-temp wheel because frozen foods are partially prepared. That means they are often cooked or baked to some degree, then flash frozen for packaging. The RTH wheel can withstand huge environmental temperature swings quickly. Traditional casters and wheels usually fail relatively quickly in this situation.
The Square Wheel
While most frequently used by medical equipment manufacturers as a medical caster, a Square Wheel Caster is best for use on relatively heavy equipment. Other challenges overcome by this square wheel include navigating minor changes in floor levels or negotiating door sills. The unique built-in ramp between the wheels helps the caster climb over such obstacles.”
Floors obstructed by the power cords, connecting wires from equipment, various and assorted tubes present a labyrinth of obstacles. As equipment gets moved around it must navigate around, over, and through this snarl of obstacles without unplugging wires; some form of “cable pusher” is desirable to preclude causing a malfunctioning piece of equipment. Cable pushers are generally found optionally incorporated onto twin-wheel casters; traditional single wheel institutional casters do not offer this option. One way some food processing plants deal with these problems is to install a plastic device around the caster wheel. It works fine, but must be removed when the device leaves the plant floor. It will not clear door sills, and in some cases precludes access to the brake levers.
Conveyor Transfer Solutions & Inverted Application
Peter McKinnon, Managing Director of Australian-based Rotacaster, insists, “Omniwheels are a fantastic alternative to traditional conveyor wheels currently on the market. The Rotacaster wheel is made from a fully injected molded, web-like frame and over-molded polyurethane rollers. This means that the axles are fully encapsulated and there are no seams, joints, or inserted pins and significantly less downtime due to lost rollers and maintenance.”
Replacing damaged or defective traditional rollers occupies fully ten percent of the repair time in a food processing environment. Beyond conveyance, the technology for these multi-directional wheels was developed primarily as an industrial and commercial floor wheel. The fixed orientation of the main wheel, allow forward and reverse movement without fighting a swivel offset, while the peripheral rollers facilitate turning, rotational, lateral, and diagonal movement.
With 360 degree maneuverability without turning or swiveling wheels, food plants are able to achieve better directional control and tracking, precise positioning – without swivel offset correction. There are obvious safety benefits including reduced injuries, lower workers’ compensation claims, because there is no resistance due to misaligned swivel castors.
The threats to safety and quality within material handling processes businesses are more serious than ever. Lean manufacturing methodologies, kaizen event feedback, and continuous process improvement have driven many pioneers to re-invent the wheel.
The Right Wheel For The Right Industry Product Lines
Are you looking for custom manufacturing for an application?
Submit an RFQ now!