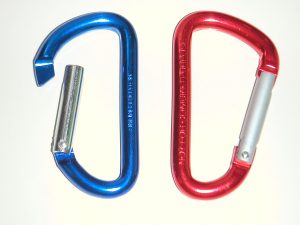
Anodized aluminum has been around for nearly a century, with some of the first documented uses of the processed metal occurring in the early 1920s when it was used to protect seaplanes from saltwater-related degradation. Since then, it’s been used in countless other applications. When compared to standard aluminum, though, anodized aluminum offers several noteworthy benefits.
What Is Anodized Aluminum?
Before we reveal the benefits of anodized aluminum, let’s go over the basics of this metal. Anodized aluminum is essential standard aluminum that’s been submerged and processed in electrolyte chemicals. Once the aluminum is placed in the electrolyte bath, an electric current is applied, thereby triggering a chemical reaction that results in the formation of a thicker layer of oxide over the aluminum.
#1) Corrosion Resistance
Anodized aluminum is more resistant to corrosion than standard aluminum. Neither standard nor anodized aluminum can rust. However, they can still corrode when exposed to moisture, air, salt or other corrosion-inhibiting compounds or elements. But anodized aluminum is less likely to corrode than standard aluminum because they have a thicker layer of oxide.
#2) Lubrication
While the single greatest benefit of anodized aluminum is its superior resistance to resistance, it also features better lubrication than standard aluminum. With aluminum is anodized, it creates deeper pores in the metal that allow for greater retention of lubricating oil or film. Standard aluminum has a smooth surface, so it’s unable to retain lubricating oil or film.
#3) Dyeing
Anodized aluminum can also be dyed to produce colorful aluminum products. Standard aluminum typically doesn’t support dyeing. As a result, companies that use standard aluminum are restricted to its natural chrome color. Thankfully, this problem is easily solved by using anodized aluminum. Unlike standard aluminum, anodized aluminum can be dyed to achieve any color or combination of colors. How is anodized aluminum able to support dyeing? When aluminum is anodized, it’s exposed to acid chemicals like sulfuric acid that trigger the formation of a thicker oxide layer as well as a porous surface. The porous surface allows anodized aluminum to hold dye more effectively than the smooth, nonporous surface of standard aluminum.
#4) Increased Adhesion
Finally, anodized aluminum offers greater adhesion for adhesives and primers. This is because the oxide surface of anodized aluminum has deeper pores that of standard aluminum. The pores are essentially holes in which adhesive, primers or liquids will flow when applied to the surface. As the anodized aluminum soaks up the liquids, it allows for greater adhesion.
No tags for this post.