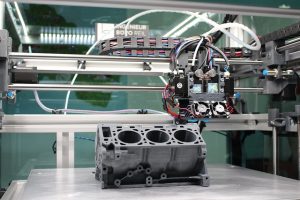
Have you heard of fused filament fabrication (FFF)? Also known as filament freeform fabrication, it’s a popular 3D printing process that’s characterized by the use of a continuous plastic filament. It involves the use of a 3D printer that guides the filament through an extruder header, after which the material is deposited onto the workpiece. To learn more about FFF and how it works, keep reading. In this post, we’re going to explore five facts about FFF.
#1) It’s the Most Popular 3D Printing Process
Although there are several types of 3D printing processes — stereolithography (SLA), selective laser sintering (SLS), etc. — none are more popular than FFF. Statistics show nearly half of all 3D printing applications involve FFF. What’s even more impressive is that FFF is a relatively new 3D printing process. It was pioneered after SLA, SLS and many other 3D printing processes.
#2) It’s Inexpensive
One of the reasons why FFF is such a popular 3D printing process is because it’s inexpensive. All 3D printing processes require a monetary investment. Manufacturing companies must purchase the equipment as well as the materials to perform them. With that said, FFF costs less than most other 3D printing processes. With its low cost, FFF has become the preferred 3D printing process among many manufacturing companies and consumers alike.
#3) It Supports a Wide Variety of Materials
FFF supports a wide variety of materials. Plastic is the most commonly used material for FFF applications. The plastic material consists of a wound spool that’s fed into an extruder header. However, FFF supports many other materials well. In addition to plastic, it supports polycarbonate (PC), high-density polyethylene (HDPE), high-impact polystyrene (HIPS), polytetrafluoroethylene (PTFE) and more. Regardless, the material is typically wound into a spool that’s connected to the 3D printer’s extruder head.
#4) Hot and Cold Ends
The extruder heads used in FFF 3D printers have a hot end and a cold end. During operation, the cold end draws the spooled material, followed by pushing the material into the hot end. The hot end of the extruder head features a heating chamber where the material is melted. As the newly melted material is ejected, it begins to solidify from exposure to the air.
#5) It Builds Layer By Layer
FFF works by building individual layers of material. The extruder head moves both vertically and horizontally as it deposits layers of the heated material. After completing a layer, the extruder head will begin to work on the next layer. Most FFF 3D printers allow you to control the speed at which the extruder head deposits these layers of material.
Learn more about Monroe’s Additive Printing Service or get your parts printed now!
No tags for this post.