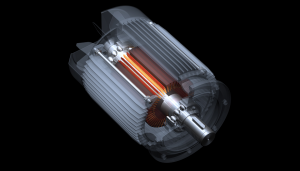
Casting processes are used extensively in the manufacturing industry to produce products and components in complex shapes. Although there are different types of casting processes, most involve pouring a liquid material, such as molten metal or heated plastic, into the center of a hollow mold. After the liquid material has cooled, it’s extracted from the mold’s cavity. With that said, investment casting is a unique casting process that’s become increasingly popular in recent years. In the past investment casting has also been known as lost-wax casting and precision casting.
Overview of Investment Casting
Investment casting is a centuries-old casting process that centers around lost-wax casting. It involves coating a wax mold with a liquid material. As the wax heats up, it begins to melt off. Molten metal is then poured into the mold’s cavity, essentially replacing the cavity’s wax with metal. Finally, the metal is allowed to cool, after which it’s separated and removed from the mold.
It’s called “investment casting” because the mold pattern used in this casting process becomes “invested” with the liquid refractory material. While other casting processes simply involve pouring liquid material into the mold’s cavity, investment casting goes one step further by surrounding the mold with the liquid material. During this initial step, the mold becomes “invested” with the liquid refractory material. Investment casting thrives in creating high precision components.
Benefits of Investment Casting
Investment casting offers several noteworthy benefits. Because it involves coating the mold with a liquid refractory material, it’s able to create products and components with an excellent surface finish. Additionally, investment casting supports a variety of materials, some of which include stainless steel, brass, titanium, carbon steel, aluminum, glass and plastic. Investment casting is considered a highly efficient process, as it creates minimal waste when compared to other common casting processes. Investment casting is highly accurate, even while producing highly intricate and precise products. The aerospace, medical and defense industry all utilize highly intricate and precise products leading to investment casting being highly utilized in those industries.
Disadvantages of Investment Casting
On the other hand, there are certain disadvantages of investment casting, one of which its high cost. Investing casting is more expensive than other casting processes, which may deter some manufacturing companies from using it. It’s also worth mentioning that investment casting doesn’t support exceptionally small or deep holes. Most investment processes can only create holes larger than 1.6 mm and shallower than 1.5 times the diameter.
Investment casting can be performed with most types of castable metals. With that said, aluminum and copper alloys are the most common types of metal used in this casting process. Regardless of which metal is used, the defining characteristic of investment casting is that it first coats the mold with the liquid refractory material, after which the mold is filled with the liquid material.