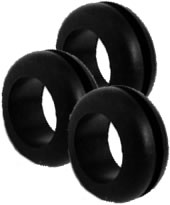
Molded rubber is used in a variety of products. You can find grommets, gaskets, hoses, boots and countless other products made of molded rubber. It’s a durable, long-lasting material that’s incredibly versatile. Unless you’re familiar with it, though, you might be wondering how molded rubber is made.
What Is Molded Rubber?
The term “molded rubber” refers to any rubber object or component that was made via a molding process. Molding processes are characterized by the use of a mold. Molds are hollow shells. To produce molded rubber, a manufacturing company will fill or inject a mold with liquified rubber.
How Rubber Is Molded
There are several different molding processes used to create molded rubber, one of the most common being compression molding. During compression molding, the mold is preheated, after which liquified rubber is poured into the mold cavity. A plug is then placed over the top of the mold cavity to seal it while subsequently applying pressure. As the liquified rubber becomes pressurized, it expands to fill all the cracks and crevasses within the mold cavity. Once the liquified rubber has cooled, it will harden so that the casting can be removed.
In addition to compression molding, injection molding is often used to make molded rubber. Injection molding lives up to its namesake by injecting liquified rubber into the mold cavity. The liquified rubber is stored inside of a heated barrel that’s placed on top of the molding machine. It’s then injected into the mold cavity through a nozzle.
A third type of molding process used to make molded rubber is transfer molding. Transfer molding is probably the most unique molding process. During transfer molding, the liquified rubber is stored in a pot that sits between the top plate and the gates. The liquified rubber will then flow into the mold cavity where it takes the same size and shape as the mold.
Benefits of Molded Rubber
Regardless of how it’s made, molded rubber offers several benefits. It’s immune to rusting and corrosion, for instance. There’s no material within molded rubber, so it can withstand humid environments without rusting or corroding.
Molded rubber is relatively inexpensive. Manufacturing companies can make it quickly and easily, and with its low cost of production, they typically sell molded rubber at a lower cost than that of other rubber materials.
Molded rubber also allows for the production of custom products and components. For custom applications such as this, a custom mold is required. As long as the mold is the correct size and shape, it will produce a product or component.
No tags for this post.