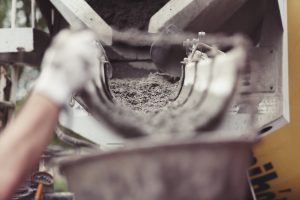
Also known as rotocasting, centrifugal casting is a casting process that’s used to create hollow cylinders. Like other casting processes, it involves the use of liquid material that’s poured into a mold. Once the liquid material has cooled and hardened, it’s removed and separated from the mold. Centrifugal casting is unique from other casting processes, however, because it uses a continuously rotating mold.
The Basics of Centrifugal Casting
With centrifugal casting, the mold is rotated as speeds of up to 3,000 rotations per minute (RPM) while the liquid material is being poured inside. After the mold has been created, it’s placed on a machine that rotates it. Next, the liquid material is poured inside the still-rotating mold.
It’s called “centrifugal casting” because it leverages the properties of centrifugal force to evenly spread the liquid material across the inside walls of the mold. As the mold spins and rotates, the liquid material is slung against the inside of the walls. Therefore, the interior of the mold remains empty and hollow, whereas a hard shell forms on the outside. The end result is a hollow cylinder with relatively thin, yet still strong, exterior.
If metal is being used as the raw material, the metal is first heated until it achieves a molten state. Next, the molten metal is poured into the rotating mold. While the mold rotates, the molten metal is flung across the interior walls. Once the molten metal cools, it turns solid and is then able to be removed as a hollow cylinder. Of course, that’s just a basic overview of how centrifugal casting works.
Benefits of Centrifugal Casting
Centrifugal casting is particularly useful for creating hollow cylinders with thin walls. Other molding processes aren’t able to achieve thin walls because they don’t use a rotating mold. The rotating mold essentially pushes the liquid material against the interior of the mold’s walls. During this process, the liquid material compresses to become thinner.
In addition to supporting thin walls, centrifugal casting also supports a wide range of materials, some of which include steel, aluminum, copper, concrete and even glass. While different materials require different techniques for casting, they all involve the use of a continuously rotating mold.
Although it’s primarily used to create hollow cylinders, centrifugal casting can be used to produce other shapes. As long as the shape features a consistent radius, it can typically be created using this casting process.