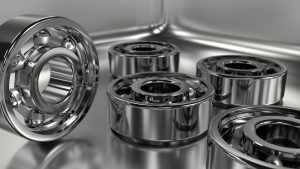
A trip through the local hardware store will show a bewildering array of colors in finished metal parts, nuts, bolts, and fasteners. Each and every difference has a reason, so let’s take a few minutes to talk about the common ways metal parts are protected from rust, corrosion, and even other metals.
It is a little known fact that some types of metal do not get along when in contact with other types of metals. Galvanic reaction caused by electrolysis means putting a stainless steel bolt together with an aluminum part may not be a good idea. One of the first reasons to coat a fastener is to prevent this effect. Rust and reaction to the atmosphere must be controlled, and in some cases, the color is there just so you can tell which coating is on the part (of course, appearance also plays a part).
Here is a description of common steel coatings and what their purpose and appearance are. While I am not including the common blueprint standards and descriptions of these items, chances are the parts you touch were made to a set standard and were measured for corrosion resistance using a “salt spray test.” This is when the part is placed in a steady salt spray and the time before corrosion begins is measured.
Chrome
Common in the ’50s and ’60s, the bright shiny luster of chrome plating also provides excellent corrosion resistance. It is quite hard because of its high nickel content, which makes it hard to scratch. Because it adds surface hardness to the steel, it was common in bumpers and latches. Chrome is expensive to apply and has a number of nasty chemicals in its process. It is not as popular as it once was but works very well in the right application.
Zinc
Zinc is very common. It comes in a variety of colors, and is very thin, so it doesn’t affect the size of the part it is put on. You may hear the term zinc chromate or zinc dichromate. They both reflect the use of hexavalent chrome solution (very nasty stuff). It is hard to scratch off. Zinc alone does not have a lot of colors, so in many cases, color is added just so you know the parts have already been plated. Zinc can be nearly clear, yellow, silver or in the case of the military… olive drab green. Zinc is done in a tank with an electrical charge, it must be dipped from a rack or done in a barrel, the barrel method is much less expensive.
Phosphate and Oil
This is a combination of a dip into zinc or manganese phosphate followed by an oil soak. Also a barrel process, it makes a part dark grey in color. Effective and inexpensive, with the benefit of adding “lubricity” to the part (makes it less resistant to friction).
Hot Dip Zinc
Parts are dipped into a vat of molten zinc and a galvanic charge is added to make it adhere to the part. It adds a relatively thick coating to the part. Zinc can be applied like this before the part is processed or after. It is important to remember, cutting holes in pretreated steels means some of the edges have no protection. Probably the reason most cars rust by the little holes they drill to put the rustproofing in!
Cadmium
Thinner than zinc but with much better corrosion resistance. Cadmium is a soft white metal that is what is known as a sacrificial coating, it corrodes away protecting the parent substrate. So Cadmium is good on steel, is compatible with aluminum, and offers good lubricity so fasteners turn and torque more smoothly. Once again, dangerous chemicals and gasses in its application are a consideration.
Black Oxide
When you see a black fastener bolt or nut, it is coated with black oxide. This means it has little corrosion resistance unless coated with oil. This process gives cheap fasteners a uniform appearance. Black oxide comes off in the wash and prep for most other plating or coating. Definitely the lowest cost and least effective long term coating for the applications.
Iridite
Adds color and increased corrosion resistance to zinc or cad plated parts, colors include green black, red, blue or bronze.
Anti-corrosion coatings and platings are not to be confused with paint or powder coat. They are often used together with paint to insure a long corrosion free life. Nor are primers necessarily there to fight corrosion. If it is shiny with luster, it is Chrome. If it is monotone silver, bronze, green or yellow, it is likely zinc chromate. If it is black it is black oxide, and if it is dark dull grey it is phosphate and oil. A medium grey finish with some texture is likely hot dip zinc. So these are the basic corrosion coating and plating methods for steel. Both aluminum and stainless steel have their own specific processes… stay tuned.
You may also enjoy these articles about metal: