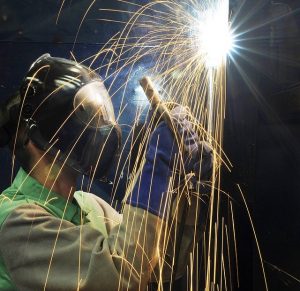
Also known as resistance spot welding, spot welding is a welding process that involves the use of an electrical current to join two or more metal surfaces. It’s typically used to join sheet metal. As the respective metal surfaces heat up, they fuse together from the heat created by the electrodes. To learn more about spot welding and how it works, keep reading.
The Basics of Spot Welding
Spot welding requires the use of copper alloy electrodes to focus an electrical current into a small area between the metal surfaces to be joined. The electrodes are also designed to create pressure, which is responsible for holding the workpieces in place. As the copper alloy electrodes create heat, the metal workpieces fuse together in a controlled manner.
There are three primary stages of spot welding. The first stage involves the application of the copper alloy electrodes on the metal workpieces. The electrical current is then stopped, though the electrodes present. Once the current has been stopped, the metal workpieces are cooled using special passages that run through the center of the copper alloy electrodes.
Advantages of Spot Welding
Spot welding offers several advantages, one of which is the ability to harden the workpieces. Because it uses heat to melt and fuse the surfaces of metal workpieces, it tends to make them harder.
Spot welding is also a fast welding process. According to Wikipedia, the average weld time for spot welding is just 0.01 to 0.63 seconds. Like with other welding processes, the weld time varies depending on the thickness of the workpieces. Thicker workpieces tend to have a longer weld time than thinner workpieces.
Disadvantages of Spot Welding
There are some potential disadvantages to spot welding, on the other hand. While spot welding increases the strength of the joined workpieces — at least at the areas where they are joined — it can cause them to warp as well. The area of the workpieces heated will essentially constrict, resulting in warpage.
Unfortunately, spot welding isn’t particularly attractive. It’s easy to see where, exactly, two workpieces have been joined with spot welding. The seams have melted material that looks messy and unattractive. Of course, not all applications require an attractive or clean weld. Nonetheless, this is a still a potential disadvantage of spot welding compared to other welding processes.
In Conclusion
There are nearly dozen different types of welding processes, one of which is spot welding. It’s called “spot welding” because it focuses the heat on a small and precise area of the workpieces to be joined.