Extrusions
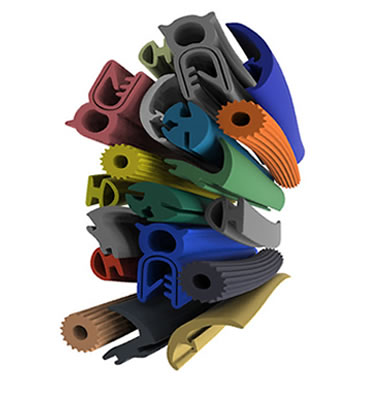
OneMonroe specializes in custom and contract manufacturing, offering a diverse range of extruded seals tailored to meet various industry needs. These high-quality extrusions are integral to numerous manufacturing processes, serving a multitude of purposes. OneMonroe's extruded seals are prominently used in the architectural sector for door and window seals, enhancing energy efficiency and weather resistance. In the automotive industry, they provide crucial sealing solutions for doors, windows, and other components, ensuring durability and performance. Additionally, these extrusions are vital in the appliance and aircraft industries, offering reliable sealing and cushioning solutions.
The applications of OneMonroe's extrusions are extensive and continually expanding with the innovation of new extrudable materials. Beyond traditional uses, these extrusions are employed in bearing seals, bumpers, and heater gaskets, proving essential for maintaining operational integrity in various machinery. Radiator overflow tubing and vacuum cleaner belts are other notable applications, where OneMonroe's products offer superior resilience and longevity. Ladder foot grips and cushions on bars or handles further illustrate the versatility of these extrusions, providing safety and comfort in everyday tools and equipment.
OneMonroe's commitment to quality and innovation ensures that their extruded seals meet the highest industry standards. These products offer numerous benefits, including enhanced durability, superior performance, and customizable options to fit specific requirements. The advanced engineering behind OneMonroe's extrusions enables them to cater to a wide array of industries, delivering reliable solutions that support efficiency and functionality. As the demand for high-performance sealing solutions grows, OneMonroe continues to lead the way with cutting-edge extrudable materials and exceptional manufacturing expertise.
Salt Batch Continuous Cure Rubber Extrusion
In this method of Rubber Extrusion, a salt mixture is used to produce the final product. The material is put into a short conveyor belt faced down into a tank, which is filled with the liquid salt mixture. The size of the tank depends upon the dimensions of the final product to be developed. The second factor that helps determines the size of the tank is the available space in the production plant and the processing speeds. The most typical size of the tank used in this method is 20cmx20cmx15m (WxDxL).
Salt Mixture
Depending upon the final product to be developed, the combination of the salt mixture may vary. However, the most common salt mixture contains Sodium Nitrite, Potassium Nitrate, and Sodium Nitrate. In this blend, Sodium Nitrate is heated to a temperature between 180 and 240°C. While using this mixture, the raw material should be pressed down underneath the surface using rollers or the conveyor belt.
In the case, the final product is complicated spray nozzles can be used to shower the salt mixture of the rubber profile. Doing this helps avoid the deformation that may occur from conveyor belts and rollers. Once the processes are completed, the remains of the salt mixtures are washed off from the product, and the product undergoes a cooling process before wind up.
Pros-The salt mixture provides fast heat transmission, resulting in the final product in less time with the best quality.
Cons-The salts in the process are classified as toxic substances. The presence of sodium nitrite can, in the event of a fire act as a fuel for combustible materials. The process of cleaning the rinsing water is difficult and time-consuming because the content of dissolved salt is huge. One of the best methods of purification is to boil the water and recycle the extra salt. These cons can be minimized if sodium nitrite is replaced by lithium nitrate.
Microwave Continuous Cure Rubber Extrusion
This method uses UHF heating to produce the final product using the heat conductance property of the rubber material. The Magnetrones in the curing equipment are located in a tunnel. These Magnetrones transmit radio waves with a frequency of 2450 MHz, which cause whirl currents in the electrically conductive materials and oscillate polar molecular structures in the material when the rubber profile passes through the conveyor belt. The heat produced so far is then maintained in a long hot-air tunnel where the actual curing process takes place. The air temperature in the tunnel is over 200°C.
Once the product has come into the desired shape, the cooling and the wind-up process is carried out, which is similar to the process followed in the Salt Batch Continuous Cure Rubber Extrusion process.
Basic Rubber Requirement
As rubber is not a good conductor of heat, to ensure this method works efficiently the rubber material must be electrically conductive and have polar molecular structures. The black reinforced rubber has carbon black filler, so it is capable of conducting heat through the induced whirl currents.
However, if you need to produce the light colored rubber products via this rubber extrusion method then ensure adding some polar material to the raw rubber compound. For example, you can add Nitrile, chloroprene polymer, or Polyethylene glycol. Adding the polar material will help conduct the heat, but in comparison with the black carbon filled rubber, it will be less.
When to use Microwave Continuous Cure Rubber Extrusion
This method takes a long time to produce the final products; hence, it should be used to develop thick-walled products. In the case, the raw material has pollutants like metal filings or poorly distributed carbon black they may result in hot spot when the rubber profile is being produced.
Pros - This method produces less environmental hazards than the other methods of extrusion.
Cons - It takes more time in the production.
Autoclave Cure Rubber Extrusion
It is a method used to produce large or custom formed parts using round pans or large trays and autoclave, a large pressurized and steam-heated vessel. If a customer wants it with a bend — we ship it with a bend.
This method can also be used to avoid collapsing of the rubber profile during the production. A former is employed in the process; therefore, it is also called former curing.
Pros - This method is useful when you need to develop large products.
Cons - You are limited to the length of the profile, as the length of the autoclave is short. Some profiles can be coil cured in an autoclave, but this imparts a curved set to the profile.
Are you looking for extrusions?
Submit an RFQ now!
Custom Manufacturing