FDM - PLA/ABS Filament (Black)
Fused filament fabrication (FFF), also known under the trademarked term fused deposition modeling (FDM), sometimes also called filament freeform fabrication, is a 3D printing process that uses a continuous filament of a thermoplastic material. Filament is fed from a large coil through a moving, heated printer extruder head, and is deposited on the growing work. The print head is moved under computer control to define the printed shape. Usually the head moves in two dimensions to deposit one horizontal plane, or layer, at a time; the work or the print head is then moved vertically by a small amount to begin a new layer. The speed of the extruder head may also be controlled to stop and start deposition and form an interrupted plane without stringing or dribbling between sections.
FEATURES
- Allows for multiple iterations at a low price
- Can be printed flat and thermoformed
- Print lines are visible
BENEFITS
- Increased market opportunities for models
- Affordable, quick prototyping
- Easy to use with no user R&D
APPLICATIONS
- Testing components for assemblies and mock-ups
- Consumer electronic components
- Snap fit assemblies
- Replace CNC machining of polypropylene and ABS to produce short-run plastic parts
- Simulate injection molded parts
- Concept and marketing models
Overview
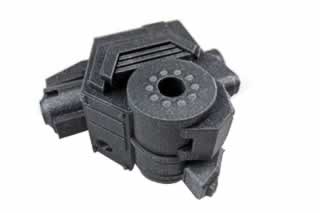
PLA Plastic or Polylactic
PLA plastic or polylactic acid is a vegetable-based plastic material, which commonly uses cornstarch as a raw material. This material is a thermoplastic aliphatic polyester and it is the primary natural raw material used in 3D printing. PLA is a fully biodegradable thermoplastic polymer consisting of renewable raw materials. Among all 3D printing materials, PLA is part of the most popular materials used for additive manufacturing.
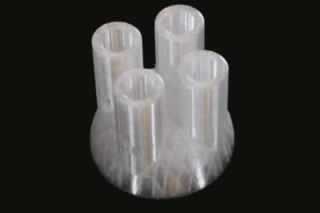
PETG
PETG is a Glycol Modified version of Polyethylene Terephthalate (PET), which is commonly used to manufacture water bottles. It is a semi-rigid material with good impact resistance, but it has a slightly softer surface which makes it prone to wear. The material also benefits from great thermal characteristics, allowing the plastic to cool efficiently with almost negligible warpage..
Options: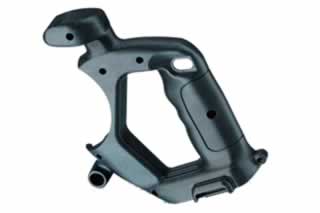
ABS (Acrylonitrile Butadiene Styrene)
ABS (Acrylonitrile Butadiene Styrene) is part of the thermoplastic polymers family. As its name implies, ABS is created from Acrylonitrile, Butadiene and Styrene polymers. It is a material commonly used in personal or household 3D printing, which is done using primarily FDM or FFF 3D printers. This common thermoplastic material is popular because it is easy to use with a desktop 3D printer, but also because it has some great material properties.
Options: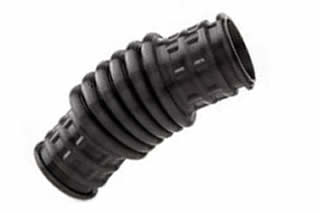
TPU
TPU 92A is a resilient thermoplastic polyurethane combining flexibility and stretch with abrasion and tear resistance. TPU 92A is an ideal replacement for applications which would traditionally use polymers as it provides a far greater level of resilience. It can be stretched or compressed and still won’t lose its shape.
Options:Are you looking for a quote for products or services?
Submit an RFQ now!