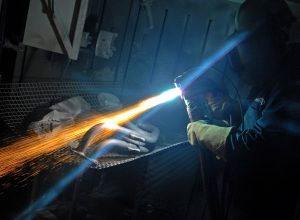
Thermal spraying is a coating process that involves the application of heated particulate matter on a surface to protect against heat, cold, electricity, moisture and rust. The particulate matter — either metal, ceramics, plastics or composites — is heated using electricity or chemicals and then sprayed onto a surface. Once complete, thermal spraying can create a thick protective outer layer measuring anywhere from 20 microns to 3 mm, all which protecting the surface from oxidation and environmental contaminants.
Plasma Thermal Spraying
One of the most common thermal spraying techniques is plasma. It’s called “plasma thermal spraying” because it uses a plasma torch to heat and spray the particulate matter onto the surface. Plasma torches, of course, are very hot, with some reaching temperatures as high as 17,500 degrees Fahrenheit. This heat melts the particulate matter while a jet shoots it onto the surface. After hitting the surface, the particulate matter spreads out and then cools, turning to a hard and solid state.
High-Velocity Oxygen Fuel Spraying
High-velocity oxygen fuel spraying (HVOF) is another thermal spraying technique. Originally developed in the 1980s, it uses heat and pressure via combustion to melt and spray particulate matter onto a surface. The benefit of HVOF is that it’s able to shoot particulate matter very fast, resulting in a strong and stable hold. HVOF is commonly used for the purpose of adding corrosion-protective layers over products and objects.
Vacuum Thermal Spraying
There’s also vacuum thermal spraying, which is a variant of plasma thermal spraying. Like the other techniques listed here, it involves heating and shooting particulate matter onto a surface. However, vacuum thermal spraying uses much lower temperatures, with most applications having a maximum temperature of just 248 degrees Fahrenheit. The low temperatures make this coating technique ideal for temperature-sensitive surfaces that can’t handle the heat of plasma thermal spraying or HVOF.
Cold Thermal Spraying
Perhaps the newest thermal spraying technique is cold spraying. Also known as gas dynamic spraying, it was pioneered by the Russian government in the 1990s and uses gas to spray particulate matter at high speeds. The high speeds allow the particulate matter to bind to surfaces, assuming they are powered by enough kinetic energy.
Thermal Spraying Applications: What You Should Know
Thermal spraying is used extensively in the construction and manufacturing industries. It can be used to protect components from rust and corrosion, for example. Even if a surface is currently susceptible to rust or corrosion, such as high-carbon steel, thermal spraying can create a protective layer that protects the surface from such degradation. Some companies use thermal spraying to increase or lower a surface’s thermal conductivity as well. To lower a surface’s thermal conductivity, non-conductive particulate matter is used. To increase its thermal conductivity, conductive particulate matter is used.