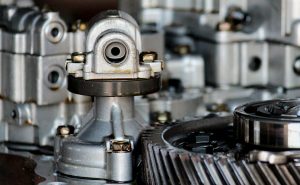
Metal injection molding is used to create a variety of small, complex products and components. Like other injection molding processes, it involves injecting heated material into a mold to form a new object in the same shape as the mold. While most other injection molding processes use rubber, plastic or similar nonmetals, metal injection molding is defined by its use of powder metal as the injection material.
#1) Steel Is Heated Up to 2,552 Degrees
For metal injection molding to work, the metal material must first be heated enough to at least partially liquefy the respective metal. Steel, for example, is often heated up to 2,552 degrees Fahrenheit, which of course is just slightly higher than its melting point. As the steel smelts, it turns into a liquid that can be injected into a mold cavity.
#2) The Market Is Growing at a CAGR of 11%
According to BCC Research, the metal injection molding is expected to grow at a compound annual growth rate (CAGR) of 11% from 2018 through 2023. So, what’s fueling the metal injection market’s growth? Well, it’s a highly effective and efficient method for manufacturing small, complex products and components.
#3) Injection ‘Shots’ Must Be Smaller Than 100 Grams
While cost effective for high-volume manufacturing applications, metal injection molding is somewhat restrictive regarding the size of the products and components it’s used to make. For example, manufacturing companies can generally only use this metalworking process to make small products and components. This is because injection “shots” — the liquefied metal that’s injected into the mold — are limited to 100 grams.
#4) It Was Invented In the 1950s
Metal injection molding didn’t gain widespread attention and usage until the 1990s, but the process itself originated in the 1950s. Around this time, Russian scientists published a paper in which they described a similar process, with the only difference being that their process involved the use of heated ceramics rather than metal. In the decades to follow, metal power was used as a substitute for ceramics, thus leading to metal injection molding.
#5) It Can Achieve Up to 99% Density
Numerous factors can affect the density of a product or component created using metal injection molding. For products and components made of steel, however, this process can achieve up to 99% density — far higher than other metalworking processes. This is important because density affects the strength and durability of objects, with denser objects being stronger and more durable than less-dense objects.