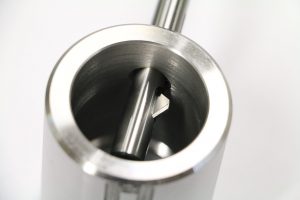
In the manufacturing industry, it’s not uncommon for workpieces to have one or more burrs after being machined. Machining operates can change the shape, size and other physical characteristics of a workpiece. Milling, for example, cuts away material from a workpiece using a rotating cutting tool. Stamping, on the other hand, involves compressing a workpiece between a die set.
When workpieces are machined, it often creates surface imperfections known as burrs. Burrs typically look like raised strands of metal and occur on areas of a workpiece that were directly exposed to a machining tool. Some burrs are harmless, but others can cause serious headache for manufacturers. As a result, many manufacturers seek to de-burr their machined workpieces.
The 3 Types of Machine-Created Burrs
Machining operations typically create one of three types of burrs, each of which features a different shape.
- Rollover: The most common type, rollover burrs resemble pieces of shaved, curled metal.
- Poisson: When excess material forms at the end of a workpiece and extends laterally, it’s called a poisson burr.
- Breakout: Finally, breakout burrs are characterized by a blossoming shape that “breaks out” from the workpiece.
You may discover other types of burrs, but most machine-related burrs consist of rollover, poisson or breakout.
De-Burring Processes
When burrs form, manufacturing companies must remove them from the workpiece using a de-burring process. There are actually several de-burring processes, each of which is designed to remove burrs.
Manufacturing companies perform manual de-burring by scraping or buffing down burrs using one or more tools. Scrubbing the surface of a workpiece with a piece of sandpaper, for example, is considered a manual de-burring process. It’s not a particularly fast or effective way to remove burrs, but it’s simple enough that anyone can do it.
A more modern and advanced way to remove burrs from a workpiece is electrochemical de-burring. With electrochemical de-burring, burrs are exposed to a solution consisting of salt or glycol. An electrical current is then applied to the solution, which dissolves the burrs. Electrochemical de-burring is highly useful for removing burrs in hard-to-reach places, such as cracks and crevasses within a workpiece.
There’s also mechanical de-burring, which involves the use of a machine to grind burrs off a workpiece. Mechanical de-burring was invented in the 1960s and has since become a popular method for removing burrs. The de-burring machine quickly and efficiently grinds off stubborn burrs, leaving behind a smooth surface on the workpiece.