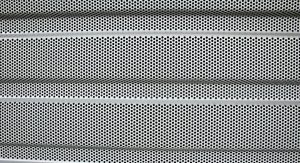
Perforation is a manufacturing process that involves scoring a workpiece or object with multiple holes. As shown in the left-hand photo, it’s typically performed on solid materials, resulting in a collection of many small holes. When a workpiece of object is perforated, it’s scored with these holes.
Perforation offers a variety of benefits. Among other things, perforated materials are more “breathable” than their non-perforated counterparts, allows for easy separation, and it allows the passage of light and fluids. While all perforation processes involve scoring a workpiece or object with multiple holes, there are three primary ways in which it’s performed.
#1) Pin Rollers
Pin rollers are frequently used by manufacturing companies to perforate workpieces and objects. With this perforation process, a cylindrical roller featuring an array of needles is rolled over a workpiece or object. Depending on the material of the workpiece or object, the needles may be hot or cold. When heated, pin rollers are able to score workpieces and objects with greater ease, especially those made of moderately hard materials.
#2) Punch and Die
In addition to pin rollers, a punch and die may also be used to perforate workpieces and objects. Punch and die perforation is frequently used in metalworking. It involves shearing the workpiece or object by pressing a punch through it as well as a die. A punch and die is capable of scoring holes in a variety of materials, including metals and alloys.
While effective, punch and die perforation creates an excessive amount of waste. The middle part of the workpiece or object is essentially scrap that must be disposed of — or recycled, at least — after being perforated with a punch and die. The perimeter of the workpiece or object is the perforated section that’s removed and used for other purposes.
#3) Laser
In recent years, laser has become an increasingly popular method of perforation among manufacturing companies. Laser, of course, involves the use of a high-powered laser to selectively melt the workpiece or object in specific areas, resulting in the creation of many small holes. When compared to pun rollers and punch and die, laser perforation offers the highest level of precision and uniformity. Laser perforation machines are expensive, however, making them somewhat restrictive for manufacturing companies.
In Conclusion
From stamps and sheet metal to wooden furniture and more, countless products feature a perforated design. Manufacturing companies typically use one of thee methods to perform perforation: pin rollers, punch and die or laser.