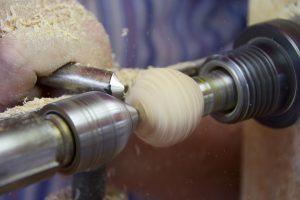
Facing is a common machining process that involves the use of a lathe or milling machine to remove material from the end and/or shoulder of a workpiece. After the workpiece is placed on the machine, a cutting tool is pressed against it at the end or shoulder. Either the workpiece or the cutting tool will turn, resulting in the removal material. By definition, facing simply involves the removal of material from the end and/or shoulder of a workpiece, but there are different types of facing operations.
Lathe Facing
Lathe facing operations are performed using a lathe. With a lathe, the workpiece rotates — at the end and/or shoulder — against a stationary cutting tool. The cutting tool itself remains fixed in the same position. Only the workpiece rotates during lathe facing operations.
Several factors can affect the performance of lathe facing operations, some of which include the following:
- Type of material from which workpiece is made.
- Size and material of cutting tool.
- Method used to hold workpiece.
- Speed at which the workpiece rotates.
Milling Facing
Milling facing operations, on the other hand, are performed using a milling machine. With a milling machine, the cutting tool rotates against the workpiece. It’s not uncommon for milling cutters to have multiple blades or teeth that grind material off the workpiece with which it’s used. Some milling machines require manual operational, whereas others are CNC controlled. Regardless, milling facing operations are characterized by the use of a milling machine to remove material from a workpiece by exposing the workpiece to a rotating cutting tool.
Facing vs Turning: Are They They Same?
Turning is a catch-all term used to describe any machining operation in which a stationary cutting tool is pressed against a rotating workpiece to remove material from the workpiece. As a result, lathe facing is a type of turning operation. With that said, however, turning operations include more than just lathe facing. They also include other operations involving the use of a lathe, including parting, grooving, boring, knurling, reaming and threading.
There are three primary types of turning operations: tapered, spherical and hard. Tapered turning operations are designed to create a cylindrical shape that becomes smaller towards the center or outside of the workpiece. Spherical turning operations are designed to create a smooth and consistent spherical shape. Finally, hard turning is designed to remove material from workpieces with a Rockwell C hardness rating of 46 or higher.