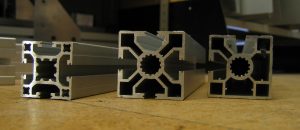
Extrusion is a manufacturing process that involves forcing material, such as heated metal, through a three-dimensional die. As shown in the image to the left, it’s used to create products or objects with a static cross-sectional profile. When the material is forced through the die, it creates a continuous line of the respective product or object. There are different types of extrusion processes, however, each of which works in a different way.
#1) Cold Extrusion
Cold extrusion is an extrusion process that’s performed using material at or near room temperature. It supports a variety of materials, including aluminum, copper, titanium, steel and tin. And because the material is forced through the die at or near room temperature, it offers higher tensile strength for the finished product or object.
#2) Warm Extrusion
As the name suggests, warm extrusion is an extrusion process that’s characterized by the use of warm, heated material. The process was invented in 1956 when a patent for the “warm extrusion of metal” was filed with the United States Patent and Trademark Office (USPTO). With that said, warm extrusion uses temperatures below the recrystallization point of the respective material. For most warm extrusion applications, the material is heated to roughly 800 to 1,800 degrees Fahrenheit.
#3) Hot Extrusion
The most common extrusion process is hot extrusion. With hot extrusion, the material is heated above its recrystallization point before it’s forced through the die. Of course, heating material above its recrystallization point makes it more malleable. As the material heats up, it becomes softer and, therefore, can squeeze through the die with greater ease. Hot extrusion is typically performed using a hydraulic press, which is capable of applying up to 100,000 pounds per square (PSI) of pressure to the heated material.
#4) Friction Extrusion
Friction extrusion is a modern extrusion process that was invented in the early 1990s. It’s unique because it involves the use of a rotating charge or billet. Other extrusion processes using a fixed, static charge or billet.
#5) Micro Extrusion
Finally, micro extrusion that’s characterized by the use of a die with an opening that’s smaller than 1 millimeter in diameter. Like friction extrusion, it’s a modern extrusion process that first appeared during the 1990s. Since then, it’s become increasingly popular in the manufacturing industry. If a company needs to produce lots of small metal products, it may use micro extrusion. The metal is first heated, after which it’s forced through a small die with an opening that’s less than 1 millimeter in diameter