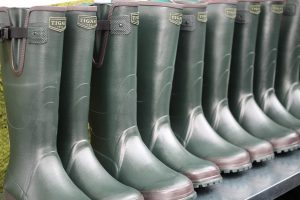
Molding is a common type of manufacturing process in which liquid material — typically plastic, rubber or other polymers — is added to a mold cavity to create a product or component. The raw material is usually heated, after which it’s added to a mold cavity. As the raw material cools, it hardens while taking the shape of the mold cavity. Not all molding processes are the same, however. Compression molding and injection molding, for instance, involve contrasting techniques. So, what’s the difference between compression molding and injection molding?
What Is Compression Molding?
Compression molding is a molding process that’s defined by its use of pressure and heat. During compression molding, the raw material is placed in the mold cavity where it’s heated. Next, plugs are inserted into the top of the mold cavity. The plugs don’t just seal the mold cavity. Rather, they are designed to pressurize it. With the raw material exposed to both heat and pressure, it begins to cure inside the mold cavity, resulting in the formation of a new product or component.
What Is Injection Molding?
Injection molding, on the other hand, is a molding process that’s defined by its use of injection technology. It’s called “injection molding” because it involves the injection of raw material into a mold cavity. During injection molding, a screw pulls the material into a hopper. As the material is heated, its injected into the mold cavity. Injection molding is similar to compression molding, with both processes involving the use of heat and pressure. The difference is that injection molding moves the material through a screw and a hopper, whereas compression molding does not.
The Benefits of Compression Molding
Each of these two common molding processes offers unique benefits for manufacturing companies. Compression molding, for instance, is a low-cost molding process that’s ideal for large-volume manufacturing applications. Compression molding also supports a wide variety of shapes and sizes. It can be used to create objects with thin or thick walls in a wide range of shapes.
The Benefits of Injection Molding
There are still reasons for manufacturing companies to consider injection molding. For example, injection molding allows for the fast and efficient production of uniform objects. Since both the pressure and heat can be precisely controlled, manufacturing companies can quickly produce many objects of the same shape and size. Injection molding also requires minimal labor.