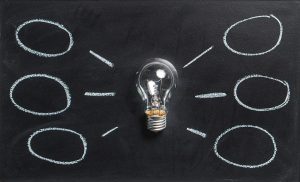
It’s not uncommon for manufacturing companies to add a layer of metal over the surface of their products or components used to make their products. Known as plating, it’s used in a variety of applications. Jewelry, for example, often contains a nickel core that’s coated in silver or gold, whereas automotive door handles contain a plastic core that’s coated in chromium. The added layer of metal protects the underlying core material from moisture while improving its appearance in the process.
While there are numerous types of plating process, most can be categorized as either electroplating or electroless plating. Both types are able to add a layer of metal over a surface, but the way in which they do so varies. So, what’s the difference between electroplating and electroless plating?
Electroplating Explained
Electroplating, by definition, is a plating process that involves the use of an electric current to bind the metal particles onto a surface. The object is first cleaned to remove any lingering dirt, dust or debris. Next, it’s submerged in a bath of the metal plating particles (and chemicals in some cases). An electric current is then applied to the object, which causes the the metal particles to attach and bind to the surface of the object.
Because electroplating uses an electric current, it only works with conductive object. If the surface of an object isn’t conductive, the electric current won’t flow through it, nor will the metal particles bind to it.
Electroless Plating Explained
As you may have guessed, electroless plating does not use an electric current to bind the metal particles onto a surface. Also known as auto-catalytic plating, it relies strictly on chemical reactions to bind metal particles onto the surface of an object. As with electroplating, the object is first cleaned. It’s then treated in various chemicals, including a catalytic solution, to induce oxidation. Once this occurs, the metal particles bind to the surface of the object. Electroless plating is a simpler plating process that eliminates the need for an electric current.
Since it doesn’t use an electric current, electroless plating works with both conductive and non-conductive objects. But electroless plating still has some drawbacks compared to its counterpart. For example, electroless plating usually requires heat — the chemicals are heated — which increases the overall cost of the process. It also produces thinner layers than electroplating. If a thick layer of metal is needed, electroplating should be considered instead.