The modern magnet is a manufactured product developed from of a naturally occurring force. The modern magnet is powerful and lightweight. It can be made in high volumes and in unique as well as standard shapes. Science has discovered a number of minerals that increase the strength of magnets and because these minerals are not plentiful and spread all over earth like coal , they are referred to as “Rare Earth Minerals” producing “Rare Earth Magnets”. Many of these mineral deposits are in Asia and it is there that most magnet production takes place. This dependence on Asia for today’s most common and useful magnets has led to efforts in other countries to develop other minerals and substances that perform as well. Modern magnets are made from a “cocktail” of minerals which can include Iron, Neodymium, Samarium, Cobalt, and Cobalt Nickle. The production process for these “Rare Earth Magnets” has historically been patented and then licensed by large corporations like Sumitomo. As these patents expire there may be growth outside of Asia in magnet production. Magnets are so critical to electronic products that their production is considered a strategic interest for most of the world.
Here is how they are made.
1. Mined metals are combined in a specific combination then melted into Ingots using a vacuum furnace. The material has no inherent magnetism and is not magnetic at this stage, or only mildly so.
2. The Ingots are ground into a superfine powder with granules 3 to 7 microns in size. Think of this powder as millions of tiny magnets just waiting to be aligned and energized.
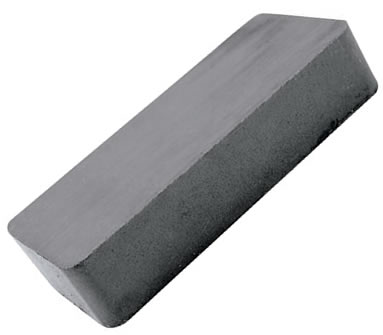
3. The powder is put in a press and forced into a shape while a magnetic field is applied using electrical current. Shapes such as rods, blocks, and strips can be produced. The addition of an “electromagnetic field causes all the tiny, powdered granules to align in the same direction creating the “polarity” necessary for the magnet to work and greatly increasing the force it can exert. While this current is strong enough to align the particles our pressed powder Ingot is not yet a magnet.
4. No matter how much force is exerted the powdered metals in the recipe must be heated to just below the melting point to become completely incorporated into each other. This is known as “Sintering”.
5. The hot metal ingot is then “cooled” by a process known as “quenching”. After this point the magnet is extremely hard and brittle. Further processing such as cutting to length, rounding edges for stress relief, or making unique shapes takes place. Since the magnet is as hard as carbon tool steel this requires special tools such as diamond tipped cutters and grinders.
6. Because of being so brittle and prone to rust nearly all magnets are coated. This can be a metal coating like Nickle, rubber, or PTFE plastics. A dark magnet is coated with rubber or plastic, a bright one with Nickle.
7. Finally the magnet is passed through an electromagnetic field which remagnitized the rare earth minerals. Magnets are typically “charged” to a strength 3 times what the magnet is rated for.
8. The magnet is then “rated” by testing and packaged for shipment and sale.
The industrial process for producing magnets in large volumes is very expensive. The modern magnet is a commercial commodity and they are made by the billions. Since these processes are not flexible most magnets are made in standard shapes and sizes. The magnet has made the quantum leap from the Compass which enabled exploration of our Planet in 500 BC, to being a key part of the electronics that allow us to explore the universe and our future.