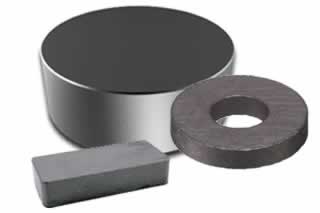
Ceramic magnets are used in countless applications. Also known as ferrite magnets, they are defined by their high iron content. All ceramic magnets are comprised primarily of iron, which is a ferromagnetic metal. Ceramic magnetics, however, typically don’t consist of solid blocks of raw iron. Rather, they require manufacturing. To learn more about the manufacturing process for ceramic magnets, keep reading.
Injection Molding
While there are different ways to manufacture them, many ceramic magnets are manufactured via injection molding. Injection molding is a molding process in which a material, such as ferromagnetic powder, is injected into a mold cavity. It follows the same basic steps as plastic injection molding. A hollow mold is hooked up to a machine that injects a material into it. In the case of ceramic magnets, a ferromagnetic material is injected into the mold cavity.
Some of the benefits of injection molding for ceramic magnets include the following:
- Supports complex shapes
- Offers tight tolerances
- Ensures a smooth surface
- Can be used for mass-manufacturing
Pressing
In addition to injection molding, some ceramic magnets are manufactured by pressing. Pressing uses the same ferromagnetic material as its injection molding counterpart. Rather than being injected into the mold cavity, though, the ferromagnetic material is “pressed” in it. There are two primary pressing techniques used for ceramic magnets: wet and dry. Wet pressing involves the use of a water-soaked or damp ferromagnetic material, whereas dry pressing involves the use of dry a ferromatnetic material.
Pressing is typically performed in conjunction with sintering. Also known as frittage, sintering is a fusion process that involves the use of either heat or pressure. When certain materials, including ferromagnetic materials, are exposed to heat or pressure, they’ll fuse together. Ceramic magnets are oftentimes manufactured by pressing and then sintering their respective ferromagnetic materials. Sintering essentially fuses the ferromagnetic material together so that it forms a solid object.
Some of the benefits of pressing for ceramic magnets include the following:
- Allows for the production of high-grade ceramic magnets
- Supports custom shapes and sizes
- Better magnetic properties than that of injection molding
In Conclusion
Ceramic magnets are typically manufactured by either injection molding or pressing. Injection molding is a more basic process in which a mold cavity is injected with a ferromagnetic material. Pressing, on the other hand, is a manufacturing process in which a ferromagnetic material is pressed into a mold cavity and then fused together via sintering.