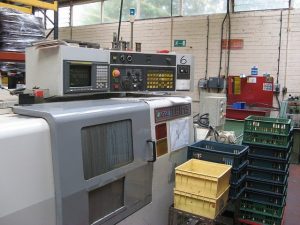
Molding processes are used in the manufacturing industry to create products and components by filling a mold cavity with material. The material is typically heated, and as it fills the mold cavity, it takes the shape of the mold. Once cooled, the casting can be removed from the mold cavity. There are many different types of molding processes, however, including rotocasting and rotational molding.
What Is Rotational Molding?
Rotational molding is a molding process in which a heated mold cavity is filled with material, after which the mold slowly rotates around two or more axes. As the mold rotates, it slings the material outwards by means of centrifugal force, thereby coating the mold cavity’s walls with the material.
There are two primary characteristics of rotational molding: First, it uses a heated mold. While most other molding processes use heated material, rotational molding goes one step further by using a heated mold. Second, rotational molding, as the name implies, uses a rotating mold. The mold isn’t stationary during this process. Rather, it slowly rotates so that the material is distributed in an even coating across the interior surface of the mold cavity.
What Is Rotocasting?
Rotocasting, on the other hand, is a molding process in which a self-curing resin is placed inside a mold cavity. Like rotational molding, rotocasting also involves the use of a rotating mold. In both processes, the filled mold rotates while subsequently slinging the material onto the inner walls of its cavity. This centrifugal force allows the material to evenly distribute, thus preventing areas in which too little or too much material is applied. The end result is a clean casting with even dimensions.
Although they both use a rotating mold, rotational molding and rotocasting aren’t the same. The difference between them lies primarily in the material which they use. Rotational molding supports traditional materials that are first heated before being poured or added to the mold cavity. In comparison, rotocasting specifically uses a self-curing resin as the material to fill the mold cavity. The self-curing resin used in rotocasting automatically hardens to form the casting.
Another difference between rotational molding and rotocasting is that the former uses a heated mold, whereas the latter uses an unheated mold. With its heated mold, rotational molding is able to achieve a low-vicious state for the material, making it easier to distribute across the mold cavity’s inner walls.
No tags for this post.