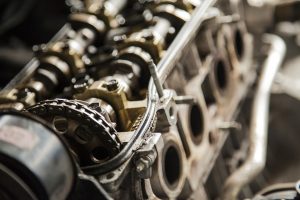
Also known as traditional die casting, high-pressure die casting is a metal casting process that involves injecting molten metal — steel, zinc, copper, aluminum, lead, magnesium, etc. — into a three-dimensional mold. The base metal is heated until it achieves a liquid, molten state. It’s then forced into the mold’s cavity, allowing it to take the shape of the mold once cooled.
High-pressure die casting is used to create everything from engine blocks to aerospace components and even heavy-duty fasteners. While there are different ways to perform it, most high-pressure die casting processes consist of the four following steps.
#1) Preparing the Mold
The first step of high-pressure die casting is mold preparation. During this initial step, the manufacturing company applies a lubricant to the interior walls of the mold. This is important because the lubricant regulates the mold’s temperature while also creating a film between the molten metal and the mold, thereby allowing for easier removal of the casting.
#2) Injection
After preparing the die mold, the manufacturing company injects it with molten metal. The mold must be completed closed and sealed during this step. Otherwise, it won’t be able to “accept” the highly pressurized molten metal. Depending on the specific application, the molten metal may be injected into the mold at a pressure of between 1,500 to 25,000 pounds per square inch (PSI). The mold maintains this pressure until the molten metal has cooled and solidified.
#3) Cavity Ejection
Next, the manufacturing company ejects the newly made cavity from the mold. The mold itself typically features ejector pins that, when engaged, release the cavity. Of course, the cavity must be solid for it to eject. If the raw metal is still liquid, the manufacturing company must wait for it to cool before it can eject the cavity from the mold.
#4) Shakeout
The fourth and final step of high-pressure die casting is shakeout. During this step, the manufacturing company separates any scrap metal from the newly created cavity. It’s not uncommon for high-pressure die casting to produce excess scrap metal. In other words, not all of the molten metal is used to create the casting. Some remains stuck inside the mold. As a result, the scrap metal must be removed before the mold can be reused.
To recap, high-pressure die casting generally consists of four steps: preparing the mold, injecting the mold with molten metal, ejecting the newly created cavity from the mold, and separating scrap metal from the cavity.