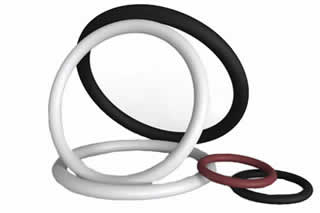
O-rings are a common component of many machines. Consisting of ring-shaped seals made of an elastomer, they are designed to prevent fluids and gases from leaking around mating surfaces. Mating surfaces are the areas where two or more passages meet. If fluid or gas flows through passages, it may leak at their mating surface. O-rings, however, prevent this from happening by creating a sealed mating surface. While all O-rings are capable of sealing mating surfaces, they are often manufactured in different ways.
#1) Extrusion
Many O-rings are made by extrusion. Extrusion is a manufacturing process in which raw material is forced through a die or series of dies. As the material goes through the die, it takes the shape of the die. For o-rings, a ring-shaped die is used.
There are different forms of extrusion. Some of them involve the use of a hopper. In other words, the raw material is fed into a hopper where it’s heated. After being heated, the raw material is then forced through a die or series of dies. Other forms of extrusion include cold extrusion, friction extrusion and microextrusion.
#2) Pressure Molding
Another manufacturing process used to create O-rings is pressure molding. Also known as compression molding, it involves the use of heat and pressure to create three-dimensional objects. To create O-rings, some manufacturing companies inject preheated material, such as rubber, into a mold cavity. The mold cavity is then fitted with a plug on top, which is able to pressure the mold cavity. As pressure increases inside of the mold cavity, the preheated material takes the shape of the mold cavity.
#3) Transfer Molding
Some O-rings are created by transfer molding. Transfer molding is similar to pressure molding. With both manufacturing processes, preheated material is placed inside of a mold cavity. The difference is that compression molding requires an open mold cavity, whereas transfer molding requires a closed mold cavity. Transfer molding is able to create higher pressure because of its closed mold cavity. Therefore, finished objects, such as O-rings, are often thicker and feature a more consistent design.
#4) Injection Molding
Injection molding is a manufacturing process that’s used to create O-rings. It involves injecting raw material into a mold cavity. The raw material typically comes in the form of pellets. The pellets are heated, after which the newly liquified material is injected into a mold cavity.