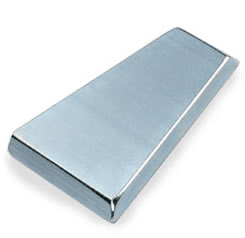
Neodymium magnets are recognized for their superior strength. They create a stronger magnetic field than that of other permanent magnets. Most neodymium magnets, in fact, are over 10 times stronger than ceramic magnets.
The problem with neodymium, however, is that it’s susceptible to corrosion. Over time, it can corrode after being exposed to oxygen and moisture. Fortunately, there are coatings available for neodymium magnets. A coating is a protective shield that prevents oxygen and moisture from reaching the magnet’s neodymium material.
Nickel
The most common type of coating for neodymium magnets is nickel. These magnets feature a thin layer of nickel over the neodymium material. Nickel is naturally resistant to oxidation. As a result, it’s often used for neodymium magnet coatings as well as electroplating applications. A nickel coating offers a protective layer against oxidation.
Chrome
In addition to nickel, chrome is commonly used as a coating for neodymium magnets. Chrome consists of a layer of chromium. Chromium, of course, is what distinguishes stainless steel from other types of steel. All stainless steels have about 11% chromium content. The presence of this chromium protects them from oxidation, including rust. When used as a coating for neodymium magnets, chromium offers similar benefits. A chrome coating will prevent oxygen and moisture from reaching the neodymium material, thus protecting the magnet from oxidation.
Copper
Some neodymium magnets are designed with a copper coating. In terms of oxidation susceptibility, copper is similar to iron. Both copper and iron can corrode, but they can’t rust. With its corrosion-resistant properties, copper is sometimes used as a coating for neodymium magnets. A layer of copper is applied over the neodymium material so that it’s protection against corrosion.
Gold
There are even neodymium magnets with a gold coating. Gold offers a higher level of protection against oxidation than copper. It doesn’t rust, nor does it corrode. Gold is actually considered one of the least reactive metals on the periodic table. With that said, there are a few disadvantages to gold coatings. For starters, gold is expensive. Neodymium magnets with a gold coating typically cost more than those with an alternative type of coating. Gold coatings can also rub off. And once the coating begins to wear down in any given area, the neodymium material will be exposed to oxygen and moisture.
Neodymium magnets typically feature a coating to protect against oxidation. The most common types of coatings for neodymium magnets include nickel, chrome, copper and gold.