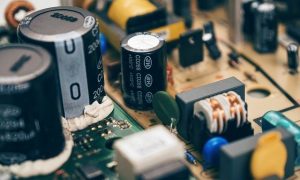
Have you heard of chemical vapor deposition? It’s a new-age manufacturing process that involves the use of vacuum technology to deposit materials onto a surface or substrate. Chemical vapor deposition is used to make a variety of products, some of which include solar panels, semiconductor thin films and more. To learn more about chemical vapor deposition and how it works, keep reading.
Overview of Chemical Vapor Deposition
Chemical vapor deposition is a process used to deposit small particles of material onto a surface or substrate using vacuum technology. During this process, a workpiece is exposed to particulate chemicals in a vacuumed environment. The vacuum pulls the chemicals to the workpiece’s surface, at which a chemical reaction occurs, thus hardening the chemicals.
Types of Chemical Vapor Deposition
By definition, chemical vapor deposition is any vacuum-based deposition process that’s used to create solid objects. There are a few different types of chemical vapor deposition, however, each of which works in a different way. Aerosol-assisted chemical vapor deposition, for example, involves the use of aerosol for the precursor. The precursor is placed in aerosol so that it’s easier to move and use.
Another common type of chemical vapor deposition is direct liquid injection. With direct liquid injection, the precursor is a liquid that’s injected into a heated chamber where it’s vaporized. An example of chemical vapor deposition is an automotive fuel injection system. Fuel injects spray fuel into a combustion chamber where the fuel is vaporized. When mixed with air and spark, the fuel vaporizes to create power that drives the vehicle. There are also plasma-based methods of chemical vapor deposition that, as the name suggests, involve the use of plasma rather than heat.
Advantages of Chemical Vapor Deposition
Over the past few decades, more and more manufacturing companies have been using chemical vapor deposition in their operations because of the unique benefits it offers. For starters, it’s a highly versatile deposition method thanks to reliance on chemical reactions. The chemicals only expand and harden when placed inside a vacuumed environment. Therefore, manufacturing companies have full control over the timing for chemical vapor deposition.
Perhaps the greatest advantage of chemical vapor deposition is its ability to create ultra-thin layers. During this process, chemicals are deposited onto a surface or substrate in small and thin layers. This makes chemical vapor deposition ideal for the production of electrical circuits, which generally require ultra-thin layers of materials.