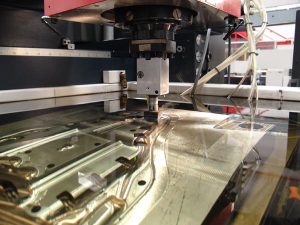
Laser cutting isn’t the method available for reshaping workpieces made of hard materials. Whether a workpiece is made of aluminum, steel or titanium, its shape can probably be manipulated using electrical discharge machining (EDM). But what exactly is EDM?
Overview of EDM
Also known as spark eroding or wire erosion, EDM is a manufacturing process that involves the use of electrical discharges — sparks created by electricity — to alter the shape or other physical properties of a workpiece. There are numerous manufacturing processes used by manufacturing companies to manipulate workpieces. Unlike most of these processes, though, EDM doesn’t rely on mechanical force. Instead, it uses heat produced by electrical discharges. When a workpiece is exposed to electrical discharges, the material from it’s made will melt. Therefore, manufacturing companies can easily manipulate otherwise hard workpieces using EDM.
EDM is performed using two electrodes. There’s a “tool” electrode as well as a “workpiece” electrode. As the voltage between these two electrodes increases, the path of the electricity changes so that it flows between them. The electrodes can then be used to selectively heat areas of a workpiece until the desired changes occur.
It’s important to note that there are several different types of EDM, the two most common of which include die sink and wire cut. Die-sink EDM is the oldest type, first appearing in the 1940s, whereas wire-cut is a newer and more modern type of EDM that was pioneered during the 1960s. With wire-cut EDM, the tool electrode is a wire. It’s a simpler method that’s particularly useful for creating metal dies.
Benefits of EDM
EDM offers several benefits for manufacturing companies. As previously mentioned, it can be used to manipulate the shape or physical properties of most materials, including hard metals like steel.
Because of the highly controlled nature of the electrical discharges used in this manufacturing processes, EDM can create very small holes or even tapered holes.
Furthermore, EDM can produce smooth and clean surfaces on workpieces. As the electrical discharges trigger, they’ll heat up the workpiece. The surface of the workpiece will then become smoother and cleaner, which is often desirable for manufacturing companies.
In Conclusion
To recap, EDM is a manufacturing process that involves the use of electrical discharges to manipulate the shape or physical properties of a workpiece. To perform it, manufacturing companies use a tool electrode and a workpiece electrode. The two electrodes produce sparks that heat up a workpiece.