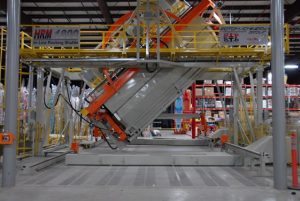
Also known as rotocasting, rotational molding is a molding process used to create hollow objects in custom shapes and sizes. While plastic injection molding is highly effective at producing solid objects in custom shapes and sizes, it doesn’t work well for hollow objects. As a result, some manufacturing companies use rotational molding for applications such as this. It offers a highly effective alternative to plastic injection that works well for hollow objects.
The Basics of Rotational Molding
Rotational molding is characterized by the use of rotational molding to create hollow objects. How does rotational molding work exactly? Although there are several types, it typically involves adding resin into a mold’s cavity. The mold, which is heated, then rotates to distribute the resin across the interior walls of the cavity.
With rotational molding, the mold’s cavity is filled with resin, after which it’s rotated. The rotational movement of the mold essentially distributes the resin evenly across the mold’s inner walls. As a result, there are no areas in which the resin is thick and thick. The resin is distributed evenly across the mold’s inner walls.
The Origins of Rotational Molding
According to Wikipedia, rotational molding has origins dating back to the mid-1800s. In 1855, Englishman R. Peters proposed the use of heat and rotational movement as a molding process. Shortly thereafter, rotational molding was used in the military and marine industries.
In the 1950s, manufacturing companies began using rotational molding to produce hollow plastic parts. Toy dolls, for example, often featured limbs made using rotational molding. Since then, rotational molding has been used to make countless other consumer and business products.
Benefits of Rotational Molding
Rotational molding offers several benefits, one of which is uniform wall thickness and density. During this molding process, the resin-filled mold will rotate. Combined with heat, this rotational movement will sling the resin across the mold’s inner walls. Rotational molding leverages the physical force of rotational movement to distribute the resin and, thus, create walls with uniform thickness and density.
In addition to uniform wall thickness and density, rotational molding is cost-effective. It typically costs less to perform rotational molding than other molding processes. The molds are inexpensive and lightweight, and aside from the machinery, it doesn’t require much else.
As previously mentioned, rotational molding supports the production of hollow objects. This is in stark contrast to many other molding processes, which typically only support the production of solid objects.