Magnetic Selection
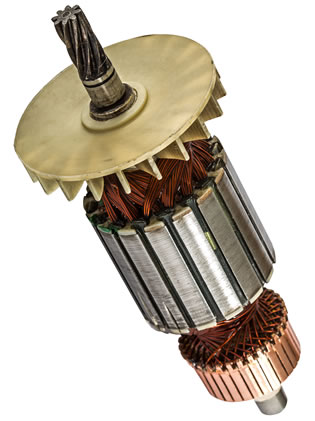
1. Work surface - The surface you will use the magnet on is important to consider. Whether it is a rough, rusty, oily, or a commonly dirty surface air gaps can develop between the magnet and part surface. This is a serious safety hazard because it reduces the holding power of the magnet.
2. Part size, thickness and weight - Just like the work surface, the size, thickness, and weight can reduce the effectiveness of the magnet holding power. If it is not the correct magnet for the size, thickness and weight this can also create the air gaps causing a safety hazard.
3. Contact area between magnet and part - The goal is to have flush contact between the magnet and the part. There are custom pole shoes that are shaped to fit the material that is being handled to achieve flush contact.
4. Air gap - Space between the part and the magnet - Having air gaps between the material and the magnet will significantly reduce the holding power and can be a safety hazard.
5. Temperature - Depending on the material of the magnet there are limitations when it comes to the temperature the magnet will be working in. For example, ceramic magnet material performs best when temperatures do not exceed 350 degrees F. Whereas a two-pole Alnico 5 magnet has a high resistance to heat up to 800 degrees F.
6. Material (Ferrous or non-ferrous) - This will depend on the metal that you are looking to use. Ferrous metal are the only ones that are magnetic, however electromagnets can use a non-ferrous metal because a magnetic field is created with an electrical current from rapid movement of electrons.
7. Continuous or intermittent operation - For continuous operation, a permanent magnet is needed since the magnet always has to remain magnetic. For intermittent operation, a temporary magnet is used since it only has a magnetic field when needed
Are you looking for magnets?
Submit an RFQ now!