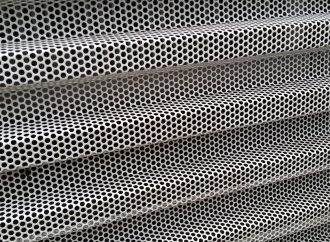
Consisting of thin and flat pieces of metal — typically steel or aluminum — sheet metal plays an important role in the construction and manufacturing industries. In the construction industry, it’s used as panels for buildings and houses. In the manufacturing industry, sheet metal is used for automobile components, heavy machinery, floors and more. When making sheet metal, however, companies often use one or more of the following forming processes.
#1) Curling
Curling is a sheet metal forming process that’s used to smooth out the otherwise sharp and rugged edges of sheet metal. Sheet metal often contains sharp edges with “burrs” after it’s initially produced. Curling is a forming process that involves de-burring sheet metal to produce smooth edges.
#2) Bending
Another common sheet metal forming process is bending. Companies typically perform bending on sheet metal using either a brake press or similar machine press. The sheet metal is placed over a die block, at which point a punch presses down onto the sheet metal. Bending doesn’t actually create holes in sheet metal. Rather, it lives up to its namesake by “bending” sheet metal in the shape of the die.
#3) Ironing
Sheet metal may also be ironed to achieve a uniform thickness. Most aluminum cans, for instance, are made of ironed aluminum. In its raw state, the aluminum sheet metal is too thick for beverage cans, so it’s ironed to achieve a thinner, more uniform composition. Ironing involves the use of a punch to force sheet metal between two dies.
#4) Laser Cutting
Laser cutting has become an increasingly common sheet metal forming process in recent years. With laser cutting, sheet metal is exposed to a high-powered laser that burns holes in the metal. It’s a faster and more precise cutting method that can even be performed automatically using a computer numerically controlled (CNC) laser cutting machine.
#5) Hydroforming
A lesser-known sheet metal forming process is hydroforming. Like deep drawing, hydroforming involves stretching the blank over a die. So, what’s the difference between hydroforming and deep drawing? The key difference between these two processes is that deep drawing requires multiple draw reductions, whereas hydroforming is performed in just one step.
#6) Punching
Finally, punching is a sheet metal forming process that involves the use of a punch and die set to create holes in sheet metal. The sheet metal is placed between the punch and die. Next, the punch presses down and through the sheet metal to create a hole.