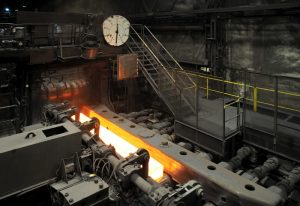
Steel mills, also known as steelworks, are industrial factories that specialize in the production of steel. They typically smelt down iron and carbon, mixing the two together in a specific ratio to create steel. Even if you’re familiar with this general concept, though, there are probably some things about steel mills you don’t know.
#1) Henry Bessemer Pioneered the Process
The origins of modern-day steel mills can be traced back to the mid-1800s, during which English inventor Henry Bessemer developed a process for creating steel by forcing air through molten iron. The air extracted most of the carbon out of the iron, leaving behind steel. Known as the Bessemer Process, it allowed for faster and more proficient production of steel, with many steel mills using this same process.
#2) Smaller Steel Mills Are Called ‘Minimills’
Not all steel mills consist of large factories. There are numerous smaller steel mills known as “minimills.” Reports show that minimills produce an average of 200,000 to 400,000 tons of steel per year. They generally receive scrap metal from recycling companies and organizations, which they smelt down and convert into steel.
#3) U.S. Steel Production Skyrocketed in the Early 20th Century
While the United States remains a leading producer of steel, the country’s steel mills were particularly busy during the early 20th century. Statistics show that in 1875, U.S. steel mills collectively produced just 380,000 tons of steel. By 1920, however, they were producing more than 60 million tons.
#4) The World’s Largest Steel Mill is a Popular Tourist Destination
It’s not uncommon for people to take tours of steel mills to see how they operate, but you might be surprised to learn just how many tourists visit the world’s largest steel mill. Located in South Korean, Gwangyang Steel Works produces more steel than any other mill in the world. In addition to pumping out an average of 18 million tons of steel annually, however, it attracts about 300,000 tourists each year.
#5) Integrated Steel Mills Perform Multiple Metalworking Processes
Some steel mills do more than just produce steel; they perform a myriad of other metalworking process. Known as an integrated steel mill, they convert iron ore to molten iron, perform metal casting, product rolling, billet rolling and more.
#6) Steel Mills Cost Billions to Build
Integrated, full-service steel mills aren’t cheap to build. While costs vary, companies generally spend around $1 billion to $4 billion to build them. But with such as a strong global demand for the metal, it can be a smart investment high profit margins.