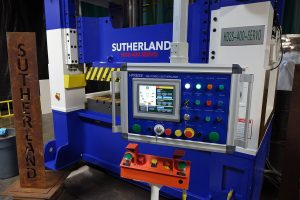
Compression molding is a molding process that’s characterized by the use of a heated mold that’s exposed to pressure. Like other molding processes, it involves placing a material, typically plastic or a similar polymer, in a mold cavity. After the material has hardened, it’s removed from the mold cavity. Compression molding is unique, however, because it leverages the power of heat and pressure. When heat and pressure are added to the process, it changes the properties of the molded workpiece.
Overview of Compression Molding
To perform compression molding, companies must first heat both the material as well the mold cavity. Once both elements have reached an appropriate temperature, the company pours the heated material into the heated mold cavity.
Heat alone causes the material as well as the mold to expand, but it’s the pressure in compression molding that truly makes this an effective molding process. After pouring the heated material into the heated mold cavity, the company closes the top of the mold with a plug. Pressure is then exerted upon the material so that it fills even the smallest open spaces in the mold cavity. In some cases, compression molding can use 1,000 to 2,000 pounds per square inch (PSI) of pressure. Combined with heat, the intense pressure pushes the material throughout the mold cavity.
After allowing the material to cool, the company then removes it from the mold cavity. While there are different techniques used in compression molding, the overall process is pretty much the same: A heated plastic or polymer material is poured into a heated mold cavity, at which point it’s exposed to pressure.
5 Things Manufacturing Companies Should Consider When Performing Compression Molding
- The amount of the plastic or polymer
- The amount of heat
- The type of heating method
- The design of the mold
- The amount of pressure
Benefits of Compression Molding
Compression molding is particularly useful for create strong, durable products. When the plastic or polymer material is exposed to heat and pressure, it becomes physically stronger than before. Injection molding can also create strong products, but it’s not as effective for this purpose as compression molding, the latter of which uses heat and pressure.
In addition to its ability to create strong and durable products, compression molding can create products in complex shapes that aren’t possible with other molding processes. As the plastic or polymer material is pressurized, it’s forced throughout the mold cavity.
Learn more other molding processes like shell molding.