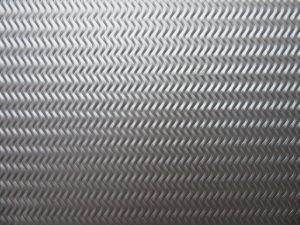
Metal parts and components are often processed to protect against corrosion. While there are different types of corrosion-inhibiting processes in metalworking, one of the most common is passivation. It’s used with a variety of different metals and alloys, including aluminum, stainless steel and even certain types of carbon steel. To learn more about passivation in metalworking, keep reading.
What Is Passivation?
Passivation is defined as a metal finishing process that’s intended to protect against corrosion. It involves the creation of an exterior layer over the surface of a metal part or component. With this exterior layer, the underlying metal won’t be directly exposed to the surrounding atmosphere. Rather, the underlying metal will be sealed, making it better protected against corrosion.
Metal corrodes as a result of oxidation. Oxidation is a chemical reaction that occurs when metal — particularly iron or iron alloys — is exposed to oxygen. There’s oxygen in the air, and there’s oxygen in the water. When exposed to air or water, metal will undergo a chemical reaction that changes its physical properties. The iron within it will essentially oxidize to create corrosion. Passivation can protect metal parts and components from corrosion by shielding them with an external layer.
The Basics of Passivation in Metalworking
Most passivation processes consist of a microcoating that’s applied over the surface of a metal part or component. For aluminum and steel, nitric oxide may be used as the microcoating. Nitric oxide will essentially dissolve the iron on the surface of the metal part or component. Iron, of course, is the precursor to corrosion. Corrosion occurs when iron is exposed to oxygen. By bathing the metal part in nitric oxide, iron will be removed from its surface. It will still contain iron deeper within its structure, but this iron won’t be directly exposed to the atmosphere, so the metal part or component shouldn’t succumb to corrosion.
Benefits of Passivation
Passivation offers a variety of benefits. For starters, it can protect most types of metal and alloys from corrosion. Corrosion is often a concern. If you’re shopping for a metal part or component, you’ll probably want it to last. If it succumbs to corrosion, you’ll inevitably have to replace it. Passivation will protect parts and components made of a metal or alloy from corrosion.
In addition to protecting metal parts and components from corrosion, passivation will remove contaminants from the surface. As previously mentioned, many forms of passivation involve the use of nitric oxide. Nitric oxide will dissolve iron on the surface of a metal part or component so that it doesn’t succumb to corrosion. A side effect of this process, however, is a cleaner surface. As the nitric oxide dissolves the superficial iron, it will remove contaminants from the surface.