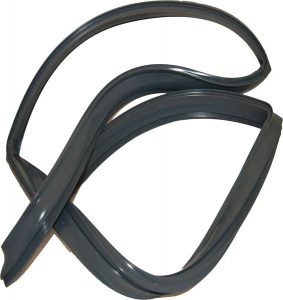
Molding is a group of manufacturing processes that involves the use of a mold to produce objects and parts in custom shapes. Dies are hollow shells that are designed to support a liquid material. The liquid material, such as heated plastic, will fill the inside of a die, thus creating a new object or part in the same shape. There are three primary types of molding processes, however, each of which is slightly different.
#1) Compression Molding
One of the most common molding processes is compression molding. As the name suggests, it’s characterized by its use of pressure. Compression molding still uses a die. After the heated liquid material has filled it, though, the die is sealed. A nozzle at the top of the die then applies pressure to the die, thus forcing the heated liquid material to expand while completely filling the die’s interior.
#2) Injection Molding
There’s also injection molding. Injection molding is similar to compression molding. Both molding processes are performed by heating a material and then injecting it into a die. As the material cools, it will harden. The casting can then be ejected or otherwise removed from inside the die.
When compared to compression molding, injection molding is better suited for simple objects and parts. It doesn’t support the same intricate shapes as compression molding. Injection molding, on the other hand, is an excellent choice for large-scale manufacturing. It can be automated to produce simple objects and parts very quickly, all while requiring little or no manual intervention.
#3) Liquid Injection Molding
Another molding process that’s used extensively in the manufacturing industry is liquid injection molding. With liquid injection mold, the die is initially heated to a specific temperature, after which liquified rubber is injected into it. It’s called “liquid injection molding” because it involves injecting liquid — specifically heated rubber — into a die or mold. As the heated rubber cools, it will create a casting in the same shape as the die.
The main difference between liquid injection molding and other molding processes is that the former uses pails or barrels of rubber materials. The pails or barrels are mixed together. Once thoroughly mixed, the material is injected into a die. Liquid injection molding takes longer to perform than other molding processes, including compression molding and injection molding. The main benefit of liquid injection molding, though, is that its cost-effective.