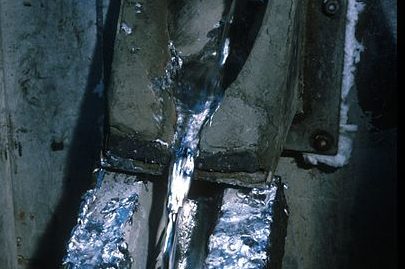
Along with sand molding, plaster molding and shell molding, evaporative-pattern casting is a common casting process used in the metalworking industry. Statistics show that it accounts for up to 29% of all aluminum casting performed in the United States. But evaporative-pattern casting differs from conventional casting processes, and it’s important to understand how it works.
Overview of Evaporative-Pattern Casting
Evaporative-pattern casting is unique because of its ability to create patterns through evaporation. Molten metal is poured into a pre-shaped mold, and when the metal cools, it creates a pattern.
The molds used in evaporative-pattern casting are typically made of foam. Once the fiery-hot molten metal reaches enters the mold, it vaporizes the foam material from which it’s made to create a distinct pattern. While different types of foam materials can be used to make the molds, evaporative-pattern casting typically involves the use of polystyrene foam.
Lost-Foam vs Full-Mold Evaporative-Pattern Casting
There are two primary types of evaporative-pattern casting: lost-foam and full-mold. While both types involve pouring molten metal into a pre-shaped mold to force the mold’s material to evaporate, they use different types of sand to perform this task. Lost-foam evaporative-pattern casting uses unbonded sand, whereas full-mold evaporative-pattern casting uses bonded sand. Other than this nuance, the two processes are pretty much the same.
Advantages of Evaporative-Pattern Casting
- Easier to perform than other types of casting processes
- Supports a wide range of shapes and sizes
- Increases thermal and abrasion resistance
- Low material and operational costs
- Supports ferrous and non-ferrous metals
- The process is widely documented, with guides revealing the step-by-step process
- High level of accuracy
History of Evaporative-Pattern Casting
The origins of evaporative-pattern casting can be traced back to the mid-1950s, during which American inventor Harold F. Shroyer filed a patent with the United States Patent and Trademark Office (USPTO) for a casting process that involves the use of expanded polystyrene and bonded sand to create foam patterns. Since Shroyer’s patent involved bonded sand, it’s now considered full-mold evaporative-pattern casting. Shroyer’s design, however, helped spur the creation of the lost-foam evaporative-pattern casting process.
The first true lost-foam evaporative-pattern casting didn’t appear until the 1960s. According to Wikipedia, the Robinson Foundry in Alabama was the first metalworking foundry to use this casting process. Shortly thereafter, General Motors began using cylinder heads manufactured with lost-foam evaporative-pattern casting. Since then, evaporative-pattern casting has made used to make countless other products, including other automotive components as well as industrial machines, equipment and hardware.