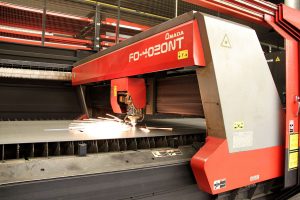
Invented in the mid-1960s, laser cutting is a type of material cutting process that involves the use of hot, high-powered lasers to cut through metal or other materials with extreme precision. The term “laser” stands for ”
Light Amplification by Stimulated Emission of Radiation,” which essentially means light with radiation. Laser cutting can be performed to cut materials in a variety of shapes and sizes, offering an unparalleled level of versatility for manufacturers. But there are different types of laser cutting processes, each of which relies on a different method of operation.
Fusion
With fusion laser cutting, metal is heated until it achieves a molten state, at which point pressurized gas — typically nitrogen or argon — blows across the molten metal. Because the metal is molten, or semi-molten, the pressurized gas can slice through it with ease. Furthermore, the gas inhibits oxidation of the metal at the cutting route.
Vaporization
Another type of laser cutting process is vaporization. With vaporization, a laser beam is affixed to a static area of the metal or material. As the laser remains in place, it heats up the metal or material until it begins to boil, thus creating a small hole. And as this hole deepens, the metal releases vapor that erodes and breaks down the adjacent walls.
Laser Flame
Also known as reactive cutting, laser flame cutting involves the oxidation triggered by gas to cut through metal or materials. It’s similar to welding via an oxygen torch, with the only difference being that a laser is used as the heating source instead of an oxygen-fed flame. Laser flame is effective because it leverages the oxidative power of reactive gas like oxygen. The metal or material is first exposed to a reactive gas, after which a laser is applied to it. The presence of this laser triggers a chemical reaction in the gas, allowing for easier and quicker cutting.
Thermal Stress
Also known as fracture-controlled cutting, thermal stress cutting is a unique type of laser cutting process. It involves the use of hot, high-powered lasers on a brittle metal or material to selectively create cracks. The brittle properties of certain metals and materials make them prone to cracking when exposed to laser. As the laser heats up the metal or material, it forms a crack, which can spread to other areas of the metal depending on where the laser is applied. Of course, the downside to thermal stress laser cutting is that it only works with brittle metals and material. Strong, durable metals and materials won’t crack under this process, thus restricting the utility of this cutting process.