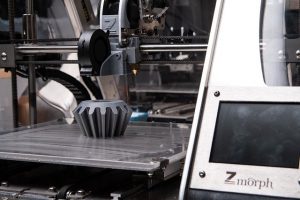
Modeling is an essential step in 3D printing. Before a 3D printer can build an object — a process that typically occurs layer by layer — a digital model of the respective object must be designed. Only after the model has been designed can the 3D printer begin to build the object. If you’re new to the field of 3D printing, though, you might be wondering how exactly object models are designed. While there’s no one-size-fits-all modeling solution, most 3D printing applications use a similar process for modeling, which we’re going to discuss in the following post.
CAD
The most common way object models are designed for 3D printing is with computer-aided design (CAD) software. CAD allows engineers and workers to design three-dimensional, as well as two-dimensional, object models using a computer. Once installed, the software serves as a digital “sandbox” for designing object models. Engineers and workers can design their object models in the CAD software, after which they can upload or transfer the finished files to a 3D printer.
3D Scanner
While not as common as CAD software, some 3D printers support the use of a scanner for object modeling. Known as a 3D scanner, it’s designed to scan an existing tangible object while saving the specifications of the object’s physical dimensions to a computer or storage drive. If an engineer wants to replicate an existing object, for instance, he or she may use a 3D scanner. The 3D scanner will create a digital copy of the object, which the 3D printer can physically build using this data.
Photogrammetry Software
Another way that object models are designed for 3D printing is with photogrammetry software. Photogrammetry software is designed to convert digital images into three-dimensional object models. It works in conjunction with photos taken of an object. The software will then analyze the photos to calculate the object’s dimensions. The finished file then be used in a 3D printer to build the object.
While CAD, 3D scanners and photogrammetry software are all used to design object models for 3D printing, CAD is by far the most popular solution. Not only is it supported by most 3D printers, but it’s better protected against errors than other modeling solutions. Prior to creating an STL file in CAD software, the model must be checked for errors. If a design suffers from errors, noise shells, manifold defects or other errors, it will appear during this verification step. As a result, CAD is more accurate and less susceptible to errors than other modeling solutions for 3D printing.