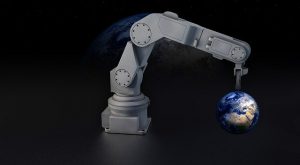
It’s a common assumption that all additive manufacturing processes require the use of solid material. A subset of 3D printing, additive manufacturing involves the construction of an object from a computer-generated file by depositing or “adding” material onto a bed or substrate. It leverages a 3D printer that releases the material out of a nozzle. While most additive manufacturing processes do, in fact, use solid material, some use liquid.
What Is Liquid Additive Manufacturing?
Liquid additive manufacturing is a group of 3D printing processes that, as the name suggests, use liquid material rather than solid material to construct objects from a computer-generated file. Like other additive manufacturing processes, it requires the use of a 3D printer. The 3D printer is responsible for converting the computer-generated object model into a physical and tangible object. The difference is that liquid additive manufacturing releases liquid material from the 3D printer.
How Liquid Additive Manufacturing Works
The steps to performing liquid additive manufacturing are similar to those of other additive manufacturing processes. An object model is first designed in a computer program, after which it’s sent to a specialized 3D printer for construction. The liquid additive manufacturing 3D printer releases liquid material out of a nozzle and onto a substrate, allowing it to build the object layer by layer.
Liquid additive manufacturing 3D printers are designed specifically to release liquid material. With that said, most of them use silicone rubber as the raw material from which they build objects. The silicone rubber material is heated within the 3D printer. Upon reaching an appropriate temperature, it turns from a solid state into a liquid state. The liquified silicone rubber is then deposited out of the 3D printer’s nozzle. As the silicone rubber collects on the underlying substrate, it forms the object.
Advantages of Liquid Additive Manufacturing
Thanks to the way in which the raw material is heated, liquid additive manufacturing is capable of producing exceptionally strong objects. When silicone rubber is heated, it becomes stronger through vulcanization. Heat forces the silicone rubber to change on a molecular level. The end result is a stronger and more resilient object.
Liquid additive manufacturing also supports the construction of objects in small sizes and complex shapes. It uses high-end, commercial-grade 3D printers that can produce countless types of objects. And with its use of liquified silicone rubber, no object is too small or too complex for liquid additive manufacturing.
Do you have a prototype that has been stuck in your head? We can help get it out of your head and into your hands with our 3D printing portal.