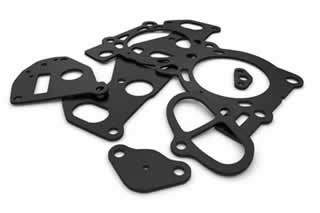
Vulcanization is a common manufacturing process used to create gaskets. It involves the use of heat, adhesive and pressure to bond two ends of rubber together. The combination of these three elements essentially fuses the rubber together, thereby forming a single and solid gasket. Vulcanized gaskets, however, are available in different splice types. Below are four of the most common splice types for vulcanized gaskets.
Butt Splice
Some vulcanized gaskets are designed with a butt splice. Butt splice is commonly used for gaskets that are exposed to little or no stress at the point of the splice. It allows for a seamless, endless construction in which the two ends of the rubber blend together.
Bevel Splice
There’s also the bevel splice. What is the bevel splice exactly? It’s an alternative splice type for vulcanized gaskets that allows for a larger surface area for the bonding process. It’s often used for gaskets that, for whatever reason, don’t support the butt splice. If a gasket’s cross-sectional area doesn’t support the butt splice, the bevel splice may be used. The bevel splice allows for a larger surface area where the two ends of the rubber meet. And with this larger surface area, the bevel splice delivers a superior level of bonding strength.
Step Splice
In terms of bonding strength, few splice types compare to the step splice. It’s stronger than both the butt splice and bevel splice. Gaskets that feature the step splice may deform under pressure or stress. With that said, the two ends typically won’t separate. The step splice is considered one of the strongest splice types for vulcanized gaskets.
Corner Splice
Finally, there’s the corner splice type. It’s not as common as the butt splice, bevel splice or step splice. Nonetheless, certain vulcanized gaskets are designed with the corner splice. The corner splice isn’t as strong as its counterparts, but it’s still capable of holding the ends of the gasket together through bonding. For sealing applications in which the gasket is exposed to minimal pressure or stress, the corner splice type be used.
Vulcanized gaskets are all made by exposing raw material — typically rubber — to heat, pressure and adhesive. Some of them, however, feature a different splice type than others. The four most common splice types for vulcanized gaskets include the butt splice, the bevel splice, the step splice and the corner splice.