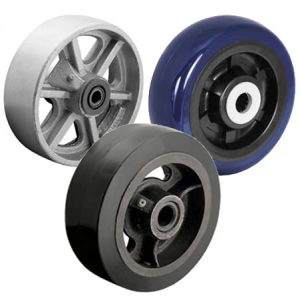
You can’t choose the right set of caster wheels without considering the bearing type. All caster wheels have a bearing. Bearings are parts or assemblies of parts that facilitate rotation. Without them, caster wheels wouldn’t be able to roll.
Ball bearings, however, are only one type of bearing available for caster wheels. Other common types of bearings for caster wheels include plain bore and roller. What’s the difference between plain bore and roller bearings exactly?
What Are Plain Bore Bearings?
Plain bore bearings are characterized by a smooth bore. Also known as sleeve bearings, they feature a simple design that’s both reliable and effective.
With a plain bore bearing, the bore of the caster wheels rides directly on the axle. The center of the caster wheels is bored out. To facilitate its rotation, the caster wheel is placed directly on an axle via its bore.
What Are Roller Bearings?
Another common type of bearing for caster wheels is roller. Also known as straight roller bearings, roller bearings feature a cage and outer sleeve. Within the cage is a set of smooth cylindrical rollers.
Differences Between Plain Bore and Roller Bearings
While they both facilitate the rotation of caster wheels, plain bore bearings and roller bearings aren’t the same. Plain bore bearings use a simpler design than their roller counterparts. They consist entirely of a smooth bore that’s placed on an axle. Roller bearings, in comparison, feature a more complex design consisting of an outer ring, cage and, most importantly, cylindrical rollers.
Aside from their design nuances, roller bearings typically support heavier loads than plain bore bearings. This is because they distribute loads more evenly than plain bore bearings. The cylindrical rollers are placed in a cage. As the caster wheel rotates, the weight of the load will be distributed throughout these rollers. Plain bore bearings, on the other hand, have a single point of contact.
Roller bearings distribute loads over a larger contact area compared to plain bore bearings. In roller bearings, cylindrical or tapered rollers are arranged in a raceway, allowing the load to be spread out across multiple points of contact. This distributes the load more evenly and reduces stress concentrations, enabling roller bearings to handle higher loads without deformation or failure.
Roller bearings require more maintenance than plain bore bearings. You’ll typically need to lubricate them to keep them rolling smoothly and prevent premature wear and tear. Since they don’t have rollers, plain bore bearings don’t require regular lubrication, making them easier to maintain.