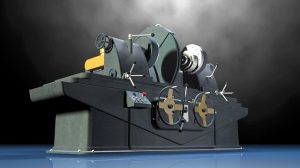
Not all metalworking processes involve welding or otherwise melting metal workpieces at high temperatures. There are cold-forming metalworking processes as well.
Also known as cold-working, cold-forming is a group of metalworking processes that involve manipulating a metal workpiece’s shape at a temperature that’s below the metal’s recrystalization point. Cold-forming metalworking processes consist of rolling, angle bending, roll forming, straightening, blanking, piercing, trimming and drawing, all of which are performed at a temperature below the metal’s recrystallization point. What are the pros and cons of cold-forming metalworking exactly?
Pros of Cold-Forming Metalworking
Because it’s often performed at room temperature, cold-forming metalworking is relatively inexpensive. Hot-forming metalworking, such as welding, requires a lot of heat. To produce this heat, energy must be consumed in the form of electricity or gas. Cold-forming metalworking, on the other hand, doesn’t require excessively hot temperatures. It’s performed either at room temperature or a temperature that’s less than the metal’s recrystalization point. Therefore, cold-forming metalworking processes cost less to perform.
Cold-forming metalworking also offers greater control over the shape and dimensions of metal workpieces than hot-forming metalworking. When metal workpieces are exposed to heat that’s greater than their recrystallizationpoint, they’ll melt. It’s difficult to control the dimensions of a melted metal workpiece. Cold-forming metalworking provides manufacturing companies with greater dimensional control by eliminating the threat of heat.
Another benefit of cold-forming metalworking is improved surface finish. Cold-working metalworking processes protect workpieces from superficial defects and imperfections.
Cons of Cold-Forming Metalworking
When compared to hot-forming metalworking, cold-forming metalworking requires greater forces to manipulate the shape of metal workpieces. Heat makes metal workpieces more malleable. With little or no heat, metal workpieces remain hard and rigid. They can still be shaped and manipulated using cold-forming metalworking, but it requires greater forces than that of hot-forming metalworking.
Before performing a cold-forming metalworking process, workpieces typically must be cleaned. The presence of dirt or contaminants could adversely affect the workpiece’s dimensions while causing undesirable results. As a result, metal workpieces are usually cleaned prior to cold-forming. This is less of a concern for hot-forming metalworking, however. Hot-forming will often separate dirt and contaminants from metal workpieces using heat.
Finally, cold-forming metalworking can lead to a phenomenon known as springback. Also known as elastic springback, it involves a cold-formed metalworkpiece “springing” back to its original shape after being deformed. With springback, a metal workpiece will return — typically only partly — to its original shape.