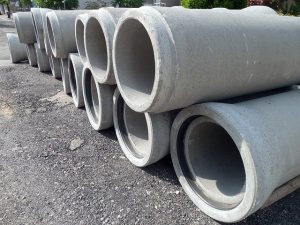
If you’ve come across centrifugal casting, you might be wondering how it differs from other casting processes. Also known as rotocasting, centrifugal casting leverages the power of centrifugal force — the physical force that occurs when an object moves in a curved direction away from its center — to create hollow, cylindrical-shaped objects. From iron and aluminum to stainless steel and even concrete, centrifugal casting supports a wide range of materials.
How Centrifugal Casting Is Performed
The first step of centrifugal casting involves pouring the liquid material — either molten metal or wet concrete — into the cavity of a spinning die. Depending on the type of machine used, the die may spin vertically, or it may spin horizontally. Regardless, the spinning die is responsible for “slinging” the liquid material across the inner walls of its cavity. As the die spins, centrifugal force distributes the liquid material evenly across the inner walls of its cavity.
Whether it’s concrete or molten metal, the liquid material used in centrifugal casting will eventually harden onto the inner walls of the mold cavity. The newly formed casting is then ejected or otherwise removed, after which it’s ready to be sold or used in other applications. Of course, that’s just the basics of centrifugal casting and how it works. Now, let’s take a look at some of the benefits of this unique casting process.
Benefits of Centrifugal Casting
Centrifugal is able to create large hollow objects that are simply not possible with other casting processes. Concrete pipes, such as those shown in the image above, are typically created using centrifugal casting.
In addition to supporting large objects, centrifugal casting is highly efficient since the dies can be used multiple times. Other types of casting processes typically use disposable dies. After the die has been used, a new one must be created. Centrifugal casting is a more efficient casting process, however, since the dies can be used multiple times.
Of course, there are no cores created with centrifugal casting, which is a good thing since it minimizes waste. With centrifugal casting, the liquid material is distributed onto the inner walls of the mold cavity. As a result, the newly formed object is hollow. Other casting processes create cores that must be disposed or recycled or after the object has been formed.
Centrifugal is just one of many casting processes used in the manufacturing industry. Others include die casting, investment casting, lost-foam casting, lost-wax casting, permanent mold casting and sand casting.