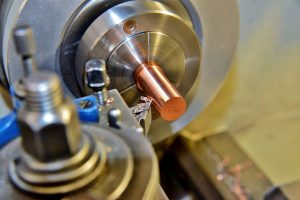
Turning operations are typically performed on cold or room-temperature metal workpieces. The workpiece is secured to a chuck, faceplate or collet that rotates the workpiece while exposing it to a stationary cutting tool. The rotation of the workpiece allows the cutting tool to selectively remove material, thereby changing the workpiece’s size and shape. There are different types of turning operations, however, one of which is hard turning.
What Is Hard Turning?
Hard turning is a turning operation that involves the use of a machine, such as a lathe, to rotate a metal workpiece against a cutting tool, but it’s designed specifically for cutting hard metals. Specifically, hard turning is intended for workpieces with a Rockwell hardness scale rating of 46 or higher. Hard metals such as this can’t be easily manipulated using conventional turning operations, so manufacturing companies used hard turning as an alternative solution.
Because it’s performed on hard workpieces, hard turning typically uses heat to soften the workpiece before rotating and exposing it to a cutting tool. With other turning operations, the workpiece is cut while cold or at room temperature. With hard turning, the workpiece is first heated to a specific temperature, after which it’s cut.
How Hard Turning Works
Hard turning is performed just like traditional turning operations, with the only exceptions being that the workpiece has a Rockwell hardness scale rating of 46 or higher and is heat treated. The workpiece is first heated to a specific temperature — the temperature varies depending on the type of metal, size of the workpiece and the application — and then it’s secured to the turning machine using a chuck, faceplate or collet. Next, the still-hot workpiece is rotated against the cutting tool, which uses a razor-sharp blade to remove material.
Benefits of Hard Turning
Hard turning offers several benefits, one of which is a low cost. When compared to other material-removal methods, such as grinding, the equipment required for hard turning typically costs less, allowing manufacturing companies to save money. Furthermore, hard turning can be performed using the same lathe as other turning operations. If a manufacturing company already performs traditional “cold” turning using a lathe, it can use that same lathe to perform hard turning.
Hard turning is also able to remove a greater amount of material than other turning operations. When the workpiece is heated, it becomes softer and, therefore, easier to cut. According to some reports, hard turning removes anywhere from 400% to 600% more material than cold turning. For applications requiring a substantial amount of material to be removed from the workpiece, hard turning is often preferred for this reason.