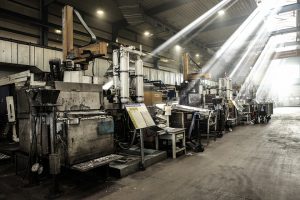
Sand casting and lost foam are two common types of evaporative-pattern casting. Also known as sand molding casting, sand casting is characterized by the use of a sand-based mold, whereas lost-foam casting is characterized by the use of a foam-based mold. In both processes, molten metal is poured into the mold, after which the newly created shell is removed. Full-mold casting, however, combines elements of both sand casting and lost-foam casting.
The Basics of Full-Mold Casting
With full-mold casting, both foam and sand are used to create the mold. The mold is first made out of foam and then cut into the desired or size and shape for the intended application. Next, the mold is coated with heat-resistant sand that binds to its foam surface.
After the mold has been prepared, molten metal is poured into the pattern’s cavity. With molten metal reaching 2,500 degrees Fahrenheit or hotter, it’s able to vaporize foam on contact. As the foam vaporizes, it creates a new object in the same shape and size as the mold pattern. The area in which the foam was located prior to being vaporized is replaced with metal. Once the molten metal cools and hardens, the newly created object is removed from the mold pattern.
Full-mold casting is most commonly used to produce automotive components like exhaust manifolds, cylinder heads and brake rotors. Of course, full-mold casting can be used for countless other applications. It’s often preferred over other molding processes because of the unique advantages it offers.
Advantages of Full-Mold Casting
- Supports complex shapes
- Highly accurate
- Highly efficient (produces little or no waste)
- Costs less than traditional wax-based casting processes
- Doesn’t require draft or flash
- Supports a variety of sizes, ranging up to several tons.
- Can be used with molten aluminum, steel, iron, copper, alloys and many other metals.
Disadvantages of Full-Mold Casting
- While relatively inexpensive when performed for high-volume applications, such as the mass-production of goods, full-mold casting typically costs more than other casting processes for low-volume applications.
- Mold patterns are susceptible to cracking and other forms of damage
Full-Mold Casting vs Sand Casting and Lost-Foam Casting
Full-mold casting isn’t the same as sand casting or lost-foam casting. Rather, it uses elements from both of these alternative evaporative-pattern casting processes. With sand casting, the molds are made entirely of sand. With lost-foam casting, the molds are made entirely of foam. Full-mold casting, on the other hand, uses a sand-covered foam mold.