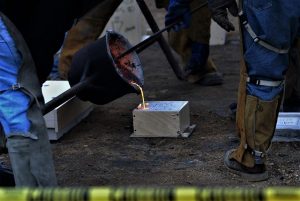
Molding processes are used to create objects with the assistance of a die. The material — which is typically heated or molten — is poured or otherwise injected into the cavity of a die. As the material fills the surrounding space, it creates a casting in the same shape as the die. Not all molding processes are the same, however. Permanent mold casting, for example, requires the use of a reusable mold. To learn more about permanent mold casting and how it works, keep reading.
Overview of Permanent Mold Casting
Also known simply as permanent molding, permanent mold casting is characterized by the use of a reusable or “permanent” mold. Rather than being disposed of, the molds can be reused. It’s not uncommon for manufacturing companies to reuse permanent molds hundreds of times.
During permanent mold casting, raw material is placed into the cavity of a permanent mold. Permanent molds are typically made of strong metals and alloys, some of which include aluminum, copper, steel, iron, graphite and lead. After the raw material has cooled and hardened, the casting is removed from the mold cavity. Because permanent mold casting uses permanent molds, the mold can then be reused.
Types of Permanent Mold Casting
Permanent mold casting can be broken down into several different types of types, one of which is gravity. As the name suggests, gravity mold casting uses gravity to inject the mold cavity with the raw material. The mold is first preheated to a temperature of up to 400 degrees Fahrenheit. Next, the mold cavity is treated with a non-sticking solution. The heated or molten raw material is then poured into the mold cavity, essentially using gravity to fill it.
Another common type of permanent mold casting is slush. Slush differs from gravity permanent mold casting in the sense that it doesn’t create solid objects. Rather, slush permanent mold casting is typically used to create hollow objects. During this casting process, heated or molten material is poured into the mold cavity. However, the material is only allowed to cool just enough so that it forms a shell around the exterior of the mold cavity. The remaining liquid material is then removed, thereby creating a hollow object.
There’s also low-pressure permanent mold casting. This alternative casting processes use low-pressure gas to force the heated or molten material into the mold cavity. It requires the use of a specialized casting machine with a plunger on top. As the plunger pushes downward, it injects the material into the mold cavity using inert gas. Neither gravity nor slush permanent mold casting use pressure.