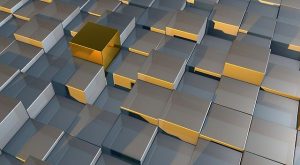
It’s not uncommon for metal products to contain a protective outer layer that discourages rust and corrosion. Steel products, for instance, almost always feature some type of protective finish. Otherwise, moisture and oxygen will cause them to rust. While there are several methods used to create a protective finish over metal workpieces, one of the most common is phosphatizing.
Overview of Phosphatizing
Also known as phosphating coating, phosphatizing is a metalworking process that involves the use of phosphoric acid to create a protective layer over a metal workpiece. It’s typically used on aluminum, silver, steel, tin and cadmium. As the phosphoric acid reacts to the metal on which it’s applied, it creates a protective outer layer, thereby protecting the underlying metal from rust and corrosion.
It may sound counterproductive, but phosphatizing actually causes corrosion — at least on the surface of the metal with which it’s used. This phosphoric acid used in this process triggers a chemical reaction with the underlying metal that results in superficial corrosion. At the same time, phosphatizing distributes phosphate crystals across the surface of the metal. The presence of these phosphate crystals essentially protects the underlying metal from further rust and corrosion.
How Phosphatizing Is Performed
To perform phosphatizing, metalworking companies begin by cleaning the metal workpiece to ensure it’s free of dirt, dust, debris or other impurities that could interfere with the process. Next, the workpiece is submerged in a bath of phosphate chemicals. As the phosphate covers the workpiece, it triggers a chemical reaction in which the dissolved salts distribute themselves evenly across the surface.
After submerging the workpiece in a bath of phosphate chemicals, the metalworking company will rinse the workpiece in a neutralizing solution. The neutralizing solution, of course, is designed to neutralize the phosphate chemicals Because the chemical reaction has occurred with its surface, the phosphate chemicals are no longer needed at this point. Therefore, they are removed by rinsing the workpiece in a neutralizing solution.
Next, the workpiece is allowed to dry. Normally, treated workpieces are air dried, during which any lingering moisture, chemicals or other liquids will evaporate.
The final step in phosphatizing is the application of lubricant or oil. Although there are exceptions, most phosphatized workpieces are treated with lubricant or oil before they are shipped and sold. Lubricant is typically applied to workpieces that will be joined with other workpieces or fasteners, whereas oil is typically used as an additional safeguard to protect against rust and corrosion.